Three-position bag welding mechanism
A three-station, welding bag technology, applied in the direction of container manufacturing machinery, paper/cardboard containers, box production operations, etc., can solve the problems of reduced operating efficiency, poor coordination, and increased process time, and achieve stable welding performance , avoid conversion, reduce the effect of auxiliary time
- Summary
- Abstract
- Description
- Claims
- Application Information
AI Technical Summary
Problems solved by technology
Method used
Image
Examples
Embodiment Construction
[0023] The present invention will be further described below in conjunction with specific examples.
[0024] See attached figure 1 to attach Figure 8 As shown, the three-station welding bag mechanism described in this embodiment includes a welding bag tube station mold 1, a welding bag head station mold 2 and a welding bag edge station mold 3, wherein the welding bag head station The mold 2 is connected in parallel between the welding bag pipe station mold 1 and the welding bag side station mold 3, and the welding bag pipe station mold 1, the welding bag head station mold 2 and the welding bag side station mold 3 are all It includes a base 4 with an upper frame 401 and a lower frame 402, a cylinder 5, an upper mold base 6 for the machine head, a lower mold base 7 for the machine head, a vacuum mold suction device 8, and a linear cam lifting and fixing mold mechanism 9, wherein, The cylinders 5 of the three station molds are installed on the respective upper frames 401 respe...
PUM
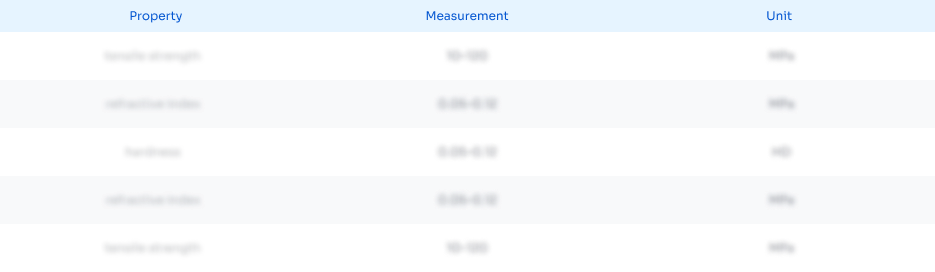
Abstract
Description
Claims
Application Information

- R&D
- Intellectual Property
- Life Sciences
- Materials
- Tech Scout
- Unparalleled Data Quality
- Higher Quality Content
- 60% Fewer Hallucinations
Browse by: Latest US Patents, China's latest patents, Technical Efficacy Thesaurus, Application Domain, Technology Topic, Popular Technical Reports.
© 2025 PatSnap. All rights reserved.Legal|Privacy policy|Modern Slavery Act Transparency Statement|Sitemap|About US| Contact US: help@patsnap.com