Control method of intelligent tension system and intelligent tension system
A technology of intelligent tensioning and control method, applied in the control of intelligent tensioning system and the field of intelligent tensioning system, can solve the problems of high failure rate of tensioning system, excessive tensioning control force, low synchronization accuracy, etc. Data measurement accuracy and construction efficiency, reducing labor intensity and improving labor efficiency
- Summary
- Abstract
- Description
- Claims
- Application Information
AI Technical Summary
Problems solved by technology
Method used
Image
Examples
Embodiment 1
[0081] like figure 1 , 4 , 5, 6, 7, and 9 are the embodiments of single pump and single roof. The intelligent tensioning system mainly includes anchorage 10, the first limiting plate 9, the first tool anchor 6, the first intelligent jack 8, the main Pumping station 1, the main pumping station 1 is connected with the first intelligent jack 8 arranged on the prestressed bundle through a plurality of oil pipes 4, the main pumping station 1 has a control cabinet, and a data acquisition instrument controlled by the control system is arranged in the control cabinet, The outer side of the first smart jack 8 is provided with a first displacement sensor 7 for measuring the extension length of the jack piston rod, and a pressure sensor 37 for measuring the pressure value of the jack is also arranged on the oil inlet road of the first smart jack 8. The main pumping station 1 The control system is electrically connected with the first displacement sensor 7 and the pressure sensor 37 of t...
Embodiment 2
[0090] like figure 2 , 8 , 10, and 11, the intelligent tensioning system mainly includes the first working anchor plate 10, the second working anchor plate 13, the first limiting plate 9, the second limiting plate 14, the first tool anchor 6, the second tool anchor Anchor 17, the first intelligent jack 8, the second intelligent jack 15, the main pumping station 1 and the auxiliary pumping station 19, the main pumping station 1 and the auxiliary pumping station 19 respectively pass through a plurality of oil pipes 4 and the first The intelligent jack 8 and the second intelligent jack 15 are connected together. Both the main pumping station 1 and the auxiliary pumping station 19 have a control cabinet, and a data acquisition instrument controlled by the control system is arranged in the control cabinet. The first intelligent jack 8 and the second intelligent jack The outer side of 15 is respectively provided with the first displacement sensor 7, the second displacement sensor ...
Embodiment 3
[0096] like image 3 , 12 , 13, and 14, that is, each pumping station is connected with one or two smart jacks, so as to realize symmetrical and synchronous tensioning of one or two bundles of steel strands at the same time, so as to improve the construction quality and work efficiency. image 3 In the shown structure, four smart jacks are used to stretch the continuous rigid structure box girder 20, wherein No. 1 and No. 3 smart tension jacks stretch a bundle of prestressed tendons, and No. 2 and No. 4 smart tension jacks Another bundle of prestressed tendons is stretched, No. 1 and No. 2 intelligent tension jacks are located at one end of the continuous rigid structure box girder 20, and No. 3 and No. 4 intelligent tension jacks are located at the other end of the continuous rigid structure box girder 20. The steps for checking the tension of different jacks in the secondary tension and the final tension are as follows: compare the tension values of the intelligent tensio...
PUM
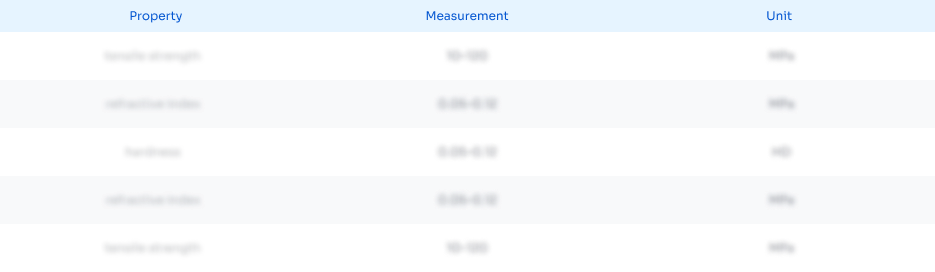
Abstract
Description
Claims
Application Information

- R&D
- Intellectual Property
- Life Sciences
- Materials
- Tech Scout
- Unparalleled Data Quality
- Higher Quality Content
- 60% Fewer Hallucinations
Browse by: Latest US Patents, China's latest patents, Technical Efficacy Thesaurus, Application Domain, Technology Topic, Popular Technical Reports.
© 2025 PatSnap. All rights reserved.Legal|Privacy policy|Modern Slavery Act Transparency Statement|Sitemap|About US| Contact US: help@patsnap.com