Synthesis method and application of submicron X-type molecular sieve
A synthesis method and molecular sieve technology, applied in the field of molecular sieves, can solve the problems of easy deactivation of adsorbents, enhanced adsorption heat accumulation, long preparation cycle, etc., to improve adsorption rate and adsorption capacity, reduce adsorption heat accumulation, and promote rapid synthesis Effect
- Summary
- Abstract
- Description
- Claims
- Application Information
AI Technical Summary
Problems solved by technology
Method used
Image
Examples
Embodiment 1
[0030] Embodiment 1, molecular sieve preparation
[0031] Directing agent preparation: Dissolve 2.5g of sodium metaaluminate, 11.3g of silica sol, and 14.0g of sodium hydroxide in deionized water, stir vigorously at 20°C for 2 hours, and let stand for 6 hours for later use.
[0032] Mother liquor preparation: Dissolve 2.5g of sodium metaaluminate, 9.6g of sodium silicate, and 3.3g of sodium hydroxide in deionized water, stir vigorously at 20°C for 2 hours, add 3g of the directing agent prepared above and 0.7g of methanol, Stirring was continued for 0.5 hours.
[0033] The obtained mother liquor was transferred into a reaction kettle lined with polytetrafluoroethylene, sealed and put into a constant temperature reactor, and aged at 70°C for 5 hours, then transferred to a microwave reactor after cooling, and continued to crystallize at 95°C for 1 hour. Centrifugal washing with deionized water to a pH value of 9-10, drying at 120°C for 2 hours, and calcining at 550°C for 4 hours...
Embodiment 2
[0038] Embodiment 2, molecular sieve preparation
[0039] Directing agent preparation: Dissolve 2.5g of sodium metaaluminate, 12.0g of silica sol, and 10.0g of sodium hydroxide in deionized water, stir vigorously at 30°C for 1.5 hours, and let stand for 6 hours for later use.
[0040] Mother liquor preparation: Take 1.6g of aluminum hydroxide, 6.4g of water glass, and 2.5g of sodium hydroxide, dissolve them in deionized water, stir vigorously at 40°C for 1.5 hours, add 3g of the directing agent prepared above and 1.0g of methanol, and continue stirring for 1 Hour.
[0041] Transfer the obtained mother liquor into a reaction kettle lined with polytetrafluoroethylene, seal it and put it into a constant temperature reactor, leave it to age at 75°C for 4.5 hours, transfer it to a microwave reactor after cooling, and continue to crystallize at 100°C for 1 hour . Centrifugal washing with deionized water to pH 9-10, drying at 110°C for 3 hours, and calcining at 600°C for 3 hours to...
Embodiment 3
[0042] Embodiment 3, molecular sieve preparation
[0043] Directing agent preparation: Dissolve 2.5g of sodium metaaluminate, 10.8g of silica sol, and 7.2g of sodium hydroxide in deionized water, stir vigorously at 30°C for 1.5 hours, and let stand for 6 hours for later use.
[0044] Mother liquor preparation: Take 1.6g of aluminum hydroxide, 6.4g of water glass, and 2.5g of sodium hydroxide, dissolve them in deionized water, stir vigorously at 10°C for 2 hours, add 3g of the directing agent prepared above and 0.6g of glycerin, Stirring was continued for 1 hour.
[0045] The obtained mother liquor was transferred into a reaction kettle lined with polytetrafluoroethylene, sealed and put into a constant temperature reactor, aged at 75°C for 5 hours, cooled and transferred to a microwave reactor, and continued to crystallize at 100°C for 1 hour. Centrifugal washing with deionized water to pH 9-10, drying at 110°C for 3 hours, and calcining at 550°C for 4 hours to obtain 13X mole...
PUM
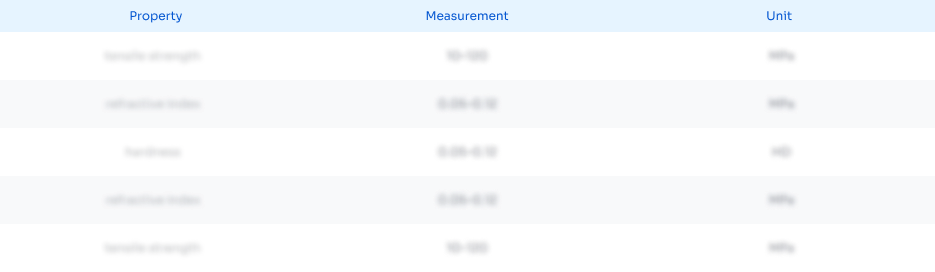
Abstract
Description
Claims
Application Information

- R&D
- Intellectual Property
- Life Sciences
- Materials
- Tech Scout
- Unparalleled Data Quality
- Higher Quality Content
- 60% Fewer Hallucinations
Browse by: Latest US Patents, China's latest patents, Technical Efficacy Thesaurus, Application Domain, Technology Topic, Popular Technical Reports.
© 2025 PatSnap. All rights reserved.Legal|Privacy policy|Modern Slavery Act Transparency Statement|Sitemap|About US| Contact US: help@patsnap.com