Method for manufacturing worsted gigging fabric
A manufacturing method and raising technology, which are applied in the field of fabric manufacturing, can solve the problems of more damage to the yarn structure, the fabric is prone to pilling, and there are many processes, so as to achieve good fluffy feeling and warmth retention, and obvious raising effect. Good effect of raising
- Summary
- Abstract
- Description
- Claims
- Application Information
AI Technical Summary
Problems solved by technology
Method used
Examples
Embodiment 1
[0018] a. Carry out pre-spinning first to obtain roving;
[0019] b. Put the roving into the spinning frame, and adjust the speed-up ratio of the pile roller group to 1.46, and obtain the spun yarn after being processed by the drafting device in turn, and finally obtain the pile single yarn after being processed by the pile roller group;
[0020] c. The piled yarn is steamed, winded, doubling with a double-thin ordinary yarn, double-twisted, and steamed in sequence, and then enters the preparation process;
[0021] d. Woven into cloth on a loom;
[0022] e. After the cloth is singed, boiled, washed, boiled continuously, and dried in sequence, it is then processed into a final shape;
[0023] f. Finally, after the finalized cloth is sheared, steamed, and continuously steamed, the fleece fabric can be obtained.
Embodiment 2
[0025] a. Carry out pre-spinning first to obtain roving;
[0026] b. Put the roving into the spinning frame, and adjust the speed-up ratio of the pile roller group to 1.55, and obtain the spun yarn after being processed by the drafting device in turn, and finally obtain the pile single yarn after being processed by the pile roller group;
[0027] c. The piled yarn is steamed, winded, doubling with a double-thin ordinary yarn, double-twisted, and steamed in sequence, and then enters the preparation process;
[0028] d. Woven into cloth on a loom;
[0029] e. After the cloth is singed, boiled, washed, boiled continuously, and dried in sequence, it is then processed into a final shape;
[0030] f. Finally, after the finalized cloth is sheared, steamed, and continuously steamed, the fleece fabric can be obtained.
Embodiment 3
[0032] a. Carry out pre-spinning first to obtain roving;
[0033] b. Put the roving into the spinning frame, and adjust the speed-up ratio of the pile roller group to 1.6, and obtain the spun yarn after being processed by the drafting device in turn, and finally obtain the pile single yarn after being processed by the pile roller group;
[0034] c. The piled yarn is steamed, winded, doubling with a double-thin ordinary yarn, double-twisted, and steamed in sequence, and then enters the preparation process;
[0035] d. Woven into cloth on a loom;
[0036] e. After the cloth is singed, boiled, washed, boiled continuously, and dried in sequence, it is then processed into a final shape;
[0037] f. Finally, after the finalized cloth is sheared, steamed, and continuously steamed, the fleece fabric can be obtained.
PUM
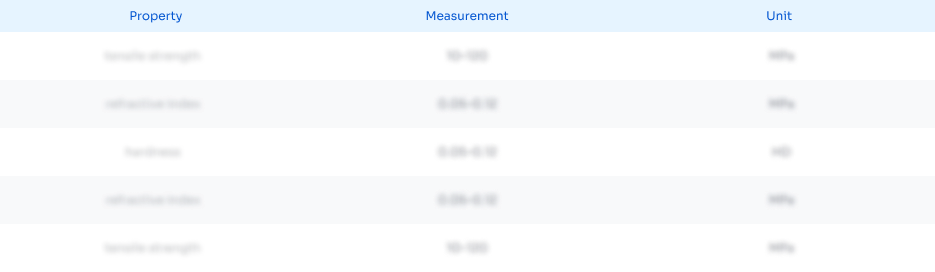
Abstract
Description
Claims
Application Information

- Generate Ideas
- Intellectual Property
- Life Sciences
- Materials
- Tech Scout
- Unparalleled Data Quality
- Higher Quality Content
- 60% Fewer Hallucinations
Browse by: Latest US Patents, China's latest patents, Technical Efficacy Thesaurus, Application Domain, Technology Topic, Popular Technical Reports.
© 2025 PatSnap. All rights reserved.Legal|Privacy policy|Modern Slavery Act Transparency Statement|Sitemap|About US| Contact US: help@patsnap.com