Method for forming front electrode of solar cell
A technology of solar cells and front electrodes, applied in the direction of copying/marking methods, circuits, photovoltaic power generation, etc., can solve the problems of semiconductor layer damage, nozzle clogging, resistance increase, etc., and achieve the effect of reducing the electrode width and increasing the amount of light
- Summary
- Abstract
- Description
- Claims
- Application Information
AI Technical Summary
Problems solved by technology
Method used
Image
Examples
Embodiment Construction
[0049] Before the description, it should be emphasized that in multiple embodiments, the same reference numerals are used for components with the same structure, and a representative description is made in the first embodiment, and the description in other embodiments is Different structure from the first embodiment.
[0050] Hereinafter, a method for forming a front electrode of a solar cell according to an embodiment of the present invention will be described in detail with reference to the drawings.
[0051] Such as figure 1 As shown, the solar cell is formed with a semiconductor layer S formed by forming an n-type semiconductor layer on the front side of a silicon substrate and a p-type semiconductor layer on the back side so as to include a pn junction interface. After coating the front surface of the semiconductor layer S with an anti-reflection film AR for minimizing reflection of light incident on the solar cell, a front electrode FE contacting the semiconductor layer...
PUM
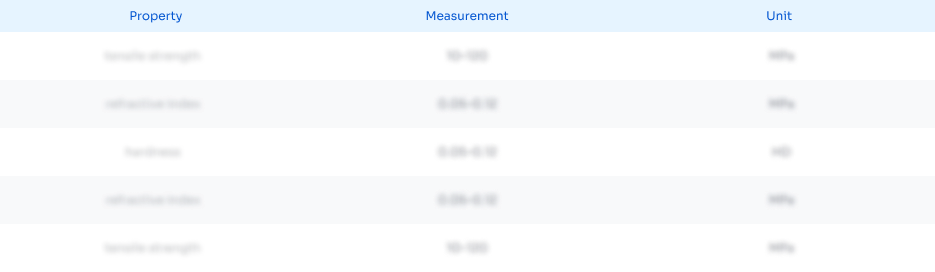
Abstract
Description
Claims
Application Information

- R&D
- Intellectual Property
- Life Sciences
- Materials
- Tech Scout
- Unparalleled Data Quality
- Higher Quality Content
- 60% Fewer Hallucinations
Browse by: Latest US Patents, China's latest patents, Technical Efficacy Thesaurus, Application Domain, Technology Topic, Popular Technical Reports.
© 2025 PatSnap. All rights reserved.Legal|Privacy policy|Modern Slavery Act Transparency Statement|Sitemap|About US| Contact US: help@patsnap.com