Modularized extrusion molding apparatus and method for section bar with order-variable cross sections
A technology of extrusion forming and cross-section, which is applied in the direction of metal extrusion dies, metal extrusion mandrels, etc., can solve the problems of difficult production of special-shaped cross-section profiles, difficult quality control, and many procedures required, and achieves easy implementation, The effect of simple equipment and short cycle
- Summary
- Abstract
- Description
- Claims
- Application Information
AI Technical Summary
Problems solved by technology
Method used
Image
Examples
specific Embodiment approach 1
[0016] Specific implementation mode one: as figure 1 As shown, 1. A modular extrusion forming device for step-variable cross-section profiles in this embodiment is characterized in that: the extrusion forming device includes a punch 1, an extrusion cylinder 2, a base 7 and at least two module (mandrel); the base 7 has a module groove 7-1 along its length direction, and the bottom of the module groove 7-1 has a discharge through hole 7-2; the at least two modules are installed in sequence from bottom to top In the module groove 7-1 of the base 7 (that is, the at least two modules are stacked), and the uppermost module is flush with the upper end surface of the base 7, each module is formed with a die opening, and the inner diameter of each die opening is determined by From bottom to top, the die mouth of each module is set coaxially and forms a stepped hole-shaped cavity (variable cross-section cavity or axial step-shaped extrusion mold cavity); the die mouth of the module at t...
specific Embodiment approach 2
[0017] Specific implementation mode two: as figure 1 As shown, the groove surfaces on both sides of the module groove 7-1 in this embodiment are in a symmetrical step shape, and the cross-sections of each module that are parallel to the cross-section of the module groove 7-1 become larger from bottom to top, and from bottom to top The stacked module groups installed in the module groove 7-1 are matched with the module groove 7-1, and each module is installed on the shoulder surface of the corresponding position. Other components and connections are the same as those in the first embodiment.
specific Embodiment approach 3
[0018] Specific implementation mode three: as figure 1 , Figure 7 ~ Figure 9 As shown, in this embodiment, each module is formed by pairing two split molds together. One split mold can be pulled out or advanced from the notch at one end of the module groove 7-1, and the other split mold can be Pull out or advance from the other end of the module slot 7-1. Other components and connections are the same as those in the second embodiment.
PUM
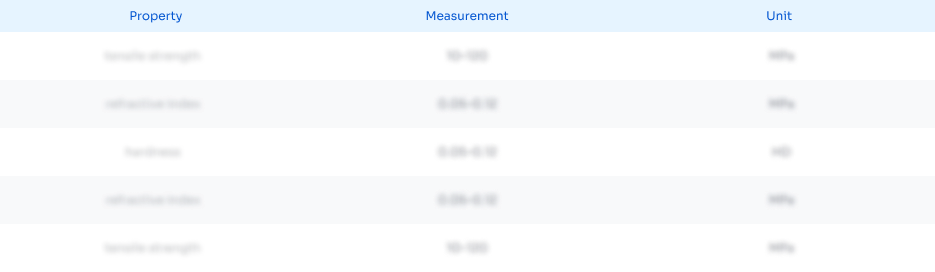
Abstract
Description
Claims
Application Information

- R&D
- Intellectual Property
- Life Sciences
- Materials
- Tech Scout
- Unparalleled Data Quality
- Higher Quality Content
- 60% Fewer Hallucinations
Browse by: Latest US Patents, China's latest patents, Technical Efficacy Thesaurus, Application Domain, Technology Topic, Popular Technical Reports.
© 2025 PatSnap. All rights reserved.Legal|Privacy policy|Modern Slavery Act Transparency Statement|Sitemap|About US| Contact US: help@patsnap.com