Thin-wall motor case milling fixture
A motor shell, thin-walled technology, used in clamping, manufacturing tools, metal processing mechanical parts, etc., can solve the problems of low production efficiency, slow processing speed, and difficult to operate, and achieve high production efficiency, high manufacturing precision, The effect of convenient workpiece clamping
- Summary
- Abstract
- Description
- Claims
- Application Information
AI Technical Summary
Problems solved by technology
Method used
Image
Examples
Embodiment 1
[0031] A thin-wall motor casing milling fixture is composed of a clamp body 1, an elastic thin-wall sleeve 2, a cylinder 3 and a clamping block 4. There are three grooves on the circumferential wall of the elastic thin-walled sleeve 2 to ensure the elasticity of the clamp body. The inner hole is designed to be tapered and installed on the clamp body 1 with screws; The outer circular surface of block 4 is designed to be tapered to match the tapered shape of the inner hole of the circumferential wall of elastic thin-walled sleeve 2, and the clamping block is enclosed within the elastic thin-walled sleeve. The workpiece is put into the elastic sleeve at the front end of the elastic thin-walled sleeve 2, and the cylinder 3 moves downward to drive the clamping block 4 to move axially. The elastic sleeve expands outwards, thereby clamping the workpiece, avoiding clamping deformation and fast clamping speed; after processing, the cylinder moves upwards, causing the elastic thin-walle...
Embodiment 2
[0033] A thin-wall motor shell milling fixture is composed of a clamp body 1, an elastic thin-wall sleeve 2, a cylinder 3, a clamping block 4 and a protective baffle 5. By selecting protective baffles 5 of different heights, the downward movement threshold value of the clamping block 4 can be set. When the clamping piece 4 moves downwards, it touches the protective baffle 5 and stops moving downwards, thereby avoiding acceleration during the clamping process. Excessive pressure produces shell deformation. The protective baffle 5 is a complete sleeve or consists of at least one separate sub-baffle. Using several separate baffles, compared with a complete sleeve, can save materials.
[0034] The connection mode between the protective baffle 5 and the side of the elastic thin-walled sleeve 2 according to the present invention is a flexible connection, sub-baffles with different heights can be selected, and can be flexibly selected for thin-walled motor casings of different mater...
Embodiment 3
[0037] A thin-wall motor shell milling fixture is composed of a clamp body 1, an elastic thin-wall sleeve 2, a cylinder 3, a clamping block 4 and a protective baffle 5. By selecting protective baffles 5 of different heights, the downward movement threshold value of the clamping block 4 can be set. When the clamping piece 4 moves downwards, it touches the protective baffle 5 and stops moving downwards, thereby avoiding acceleration during the clamping process. Excessive pressure produces shell deformation.
[0038] The inner hole of the elastic thin-walled sleeve 2 of the present invention is tapered. It can ensure that the clamping is more reliable to the greatest extent possible.
[0039] At least one groove is formed on the circumferential wall of the elastic thin-walled sleeve 2 of the present invention. Three grooves can be arranged on the circumferential wall of the elastic thin-walled sleeve 2 of the present invention. The material cost of the elastic thin-walled slee...
PUM
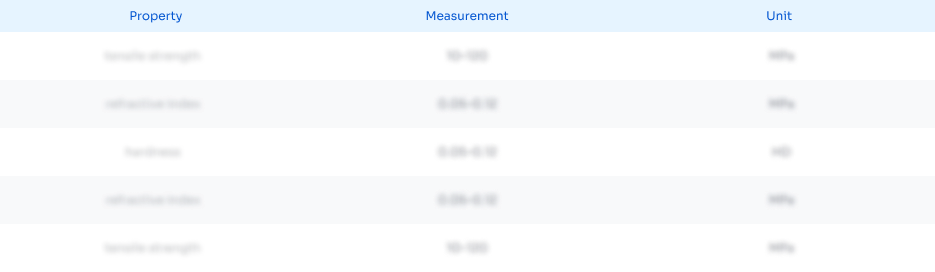
Abstract
Description
Claims
Application Information

- R&D Engineer
- R&D Manager
- IP Professional
- Industry Leading Data Capabilities
- Powerful AI technology
- Patent DNA Extraction
Browse by: Latest US Patents, China's latest patents, Technical Efficacy Thesaurus, Application Domain, Technology Topic, Popular Technical Reports.
© 2024 PatSnap. All rights reserved.Legal|Privacy policy|Modern Slavery Act Transparency Statement|Sitemap|About US| Contact US: help@patsnap.com