Purifying process of cyclobutanone
A technology for crude cyclobutanone and cyclobutanone, applied in the separation/purification of carbonyl compounds, organic chemistry, etc., can solve the problems of dichloromethane being volatile, toxic, difficult to separate, etc., and achieve mild conditions for removing impurities. Simple process and cheap effect
- Summary
- Abstract
- Description
- Claims
- Application Information
AI Technical Summary
Problems solved by technology
Method used
Examples
Embodiment 1
[0028] Add 500g of cyclobutanone crude product (content 90%, GC test) to the 1000ml reaction bottle equipped with agitator and thermometer, add 113g potassium permanganate in four times, control the temperature in the reaction bottle not to exceed 40°C, stir for 4 Hour. After the reaction is complete, add 1000 ml of ether and 500 ml of water, stir, separate the liquids, dry the organic phase, and rectify to collect fractions at 98-99°C with a content of 98.7% (GC test).
Embodiment 2
[0030] Add 500g of crude cyclobutanone (content 95%, GC test) to a 5000ml reaction flask equipped with a stirrer and a thermometer, add 85g of potassium permanganate in two times, control the inner temperature of the reaction flask at 25±2°C, and stir for 3 Hour. After the reaction is complete, add 1000 ml of ether and 500 ml of water, stir, separate the liquids, dry the organic phase, and rectify to collect fractions at 98-99°C with a content of 99.2% (GC test).
Embodiment 3
[0032] Add 500g of crude cyclobutanone (92% content, GC test) into a 1000ml reaction flask equipped with a stirrer and a thermometer, add 106g of chromium trioxide at a time, control the internal temperature of the reaction flask at 30±2°C, and stir for 6 hours. After the reaction is complete, add 1000 ml of ether and 500 ml of water, stir, separate the liquids, dry the organic phase, and rectify to collect fractions at 98-99°C with a content of 99.0% (GC test).
PUM
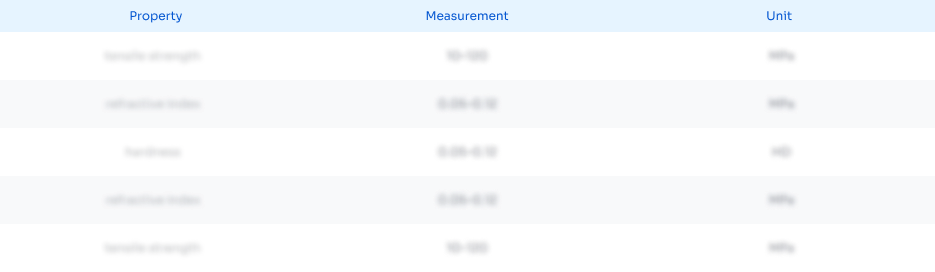
Abstract
Description
Claims
Application Information

- R&D
- Intellectual Property
- Life Sciences
- Materials
- Tech Scout
- Unparalleled Data Quality
- Higher Quality Content
- 60% Fewer Hallucinations
Browse by: Latest US Patents, China's latest patents, Technical Efficacy Thesaurus, Application Domain, Technology Topic, Popular Technical Reports.
© 2025 PatSnap. All rights reserved.Legal|Privacy policy|Modern Slavery Act Transparency Statement|Sitemap|About US| Contact US: help@patsnap.com