Blade machining process error prediction method based on extended error flow
A technology for processing and error prediction, applied in special data processing applications, instruments, electrical digital data processing, etc.
- Summary
- Abstract
- Description
- Claims
- Application Information
AI Technical Summary
Problems solved by technology
Method used
Image
Examples
Embodiment Construction
[0178] Reference Figure 1-7 . Taking a certain kind of blade (material titanium alloy TC4) parts processed by an aero engine manufacturer as an example, the error analysis and prediction of the blade processing process is carried out according to the steps. The present invention is described in detail to verify the predictive effect of the present invention on the error of a certain type of blade multi-process machining process.
[0179] Discrete the cross-section lines of the blade parts with equal precision to obtain the micro-element coordinate points, simplify the blade parts into thin-plate parts, and map the corresponding micro-element coordinate points to the simplified blade model to obtain the progress of the thin plate and the blade parts. After the discrete processing, the points correspond, and these corresponding points on the thin plate are used to approximate the corresponding points on the blade.
[0180] In the simplified model, ps 1 To ps 4 For the micro elemen...
PUM
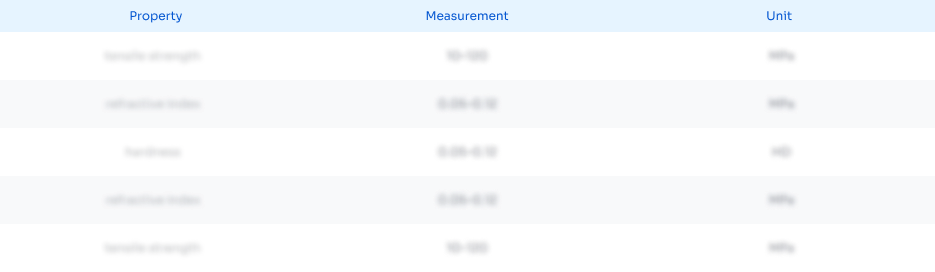
Abstract
Description
Claims
Application Information

- R&D
- Intellectual Property
- Life Sciences
- Materials
- Tech Scout
- Unparalleled Data Quality
- Higher Quality Content
- 60% Fewer Hallucinations
Browse by: Latest US Patents, China's latest patents, Technical Efficacy Thesaurus, Application Domain, Technology Topic, Popular Technical Reports.
© 2025 PatSnap. All rights reserved.Legal|Privacy policy|Modern Slavery Act Transparency Statement|Sitemap|About US| Contact US: help@patsnap.com