Defoaming machine
A defoaming machine and defoaming technology, applied in the direction of ceramic molding machines, manufacturing tools, etc., can solve the problems of waste, hollowing, poor quality of foamed cement, etc., and achieve the goal of improving production efficiency, reducing process, and saving installation space Effect
- Summary
- Abstract
- Description
- Claims
- Application Information
AI Technical Summary
Problems solved by technology
Method used
Image
Examples
Embodiment 1
[0055] Such as Figure 1-2 As shown, the defoaming machine of this embodiment includes a frame 1, on which a support plate 7 is horizontally fixed, on which a drive motor 2 is installed, and two ends of the support plate 7 are respectively fixed with The connecting steel plate 6 is equipped with a main shaft 302, and the outer surface of the main shaft 302 is evenly arranged with defoaming parts along the circumferential direction; the defoaming machine of this embodiment also includes a transmission assembly, which is connected to the drive motor 2 and the main shaft 302, It is used to transmit the driving force of the driving motor 2 to the main shaft 302 to drive the main shaft 302 to rotate. The above-mentioned support plate 7, drive motor 2, connecting steel plate 6 and transmission assembly together constitute the defoaming assembly of the defoaming machine. When the driving motor 2 is working, the main shaft 302 rotates under the action of the transmission assembly, wh...
Embodiment 2
[0077] This embodiment is a modification based on embodiment 1, and its difference from embodiment 1 is that the limiting track is a highly undulating limiting track, and when the limiting wheel 901 walks on the limiting track, Its height is constantly changing, so that the height of the main shaft 302 and the steel wire 303 on the main shaft 302 relative to the body to be defoamed is constantly changing, so that this kind of defoaming machine can be used to have a non-horizontal upper surface to prepare the upper part with a specific thickness. Foamed cement for air-bubble cleaning layer.
[0078] Specifically, set limit rails with target height undulations on both sides of the object to be defoamed, adjust the horizontal upper surface of the object to be defoamed to match the highest track position, and adjust the defoamer to the position to be defoamed by the lifting device Above the body, adjust the relative height relationship between the limit wheel 901, the limit track ...
Embodiment 3
[0080] Such as Figure 12 As shown, this embodiment is a deformation on the basis of Embodiment 1 or Embodiment 2, the difference is that the above-mentioned defoaming parts do not use steel wires, but set angle steel 309 on the defoaming main shaft, and connect nylon on the angle steel 309 The ribbon 310 , the defoaming spindle 302 drives the nylon ribbon 310 to rotate, and then performs defoaming treatment on the defoaming layer of the defoaming body.
PUM
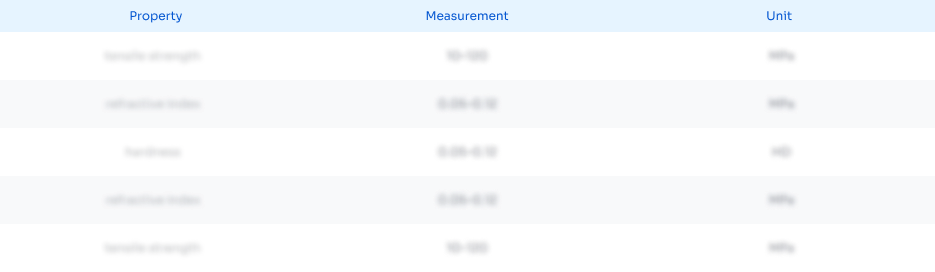
Abstract
Description
Claims
Application Information

- R&D
- Intellectual Property
- Life Sciences
- Materials
- Tech Scout
- Unparalleled Data Quality
- Higher Quality Content
- 60% Fewer Hallucinations
Browse by: Latest US Patents, China's latest patents, Technical Efficacy Thesaurus, Application Domain, Technology Topic, Popular Technical Reports.
© 2025 PatSnap. All rights reserved.Legal|Privacy policy|Modern Slavery Act Transparency Statement|Sitemap|About US| Contact US: help@patsnap.com