Processes to make water and oil repellent bcf yarn
A yarn and anti-fouling technology, applied in the field of blankets and BCF yarns with improved anti-fouling properties
- Summary
- Abstract
- Description
- Claims
- Application Information
AI Technical Summary
Problems solved by technology
Method used
Image
Examples
Embodiment 1
[0055] Embodiment 1 (comparison)
[0056] use figure 1 Two strands of 922 denier beige solution-dyed nylon 66 BCF made of cationic dyeable polymer were cable twisted at 7000 rpm on a Volkman to form a 6.0 tpi two-ply yarn. The winding speed was about 50ypm. Subsequently, the cabled yarns were heat set on a Suessen with dry air at 200°C. The residence time in the channel is about 60 seconds. The heat-treated yarn was converted to a 35 oz / sq. yd., 1 / 12 gauge, 3 / 8" pile height cut pile carpet.
Embodiment 2
[0057] Embodiment 2 (the present invention)
[0058] use figure 2 Two strands of 922 denier beige solution-dyed nylon 66 BCF made of cationic dyeable polymer were cable twisted at 7000 rpm on a Volkman to form a 6.0 tpi two-ply yarn. The winding speed was about 50ypm. Insert the chemical applicator between the take-up roll and winder as described in Figure 3 Option A. 50% A-201 antifouling chemical was applied to the cabled yarn at about 20% pick-up by weight with a ½ inch wide cotton wick (Wet Wick, Perperell MA). The cabled yarn was passed through the wet core at about 50ypm. Subsequently, the cabled yarns were heat set on a Suessen with dry air at 200°C. The residence time in the channel is about 60 seconds. The heat set yarn was analyzed to have 925 ppm fluorine. The heat-treated yarn was converted to a 35 oz / sq. yd., 1 / 12 gauge, 3 / 8" pile height cut pile carpet.
Embodiment 3
[0059] Embodiment 3 (the present invention)
[0060] use figure 2 Two strands of 922 denier beige solution-dyed nylon 66 BCF made of cationic dyeable polymer were cable twisted at 7000 rpm on a Volkman to form a 6.0 tpi two-ply yarn. The winding speed was about 50ypm. Such as figure 2 Insert the chemical applicator between the take-up roll and winder as described in . 25% A-201 stain repellant chemical was applied to the cabled yarn with a ½ inch wide cotton wick (Wet Wick, Perperell MA). The cabled yarn was passed through the wet core at about 50ypm. Subsequently, the cabled yarns were heat set on a Suessen with dry air at 200°C. The residence time in the channel is about 60 seconds. The heat set yarn was analyzed to have 445 ppm fluorine. The heat-treated yarn was converted to a 35 oz / sq. yd., 1 / 12 gauge, 3 / 8" pile height cut pile carpet.
PUM
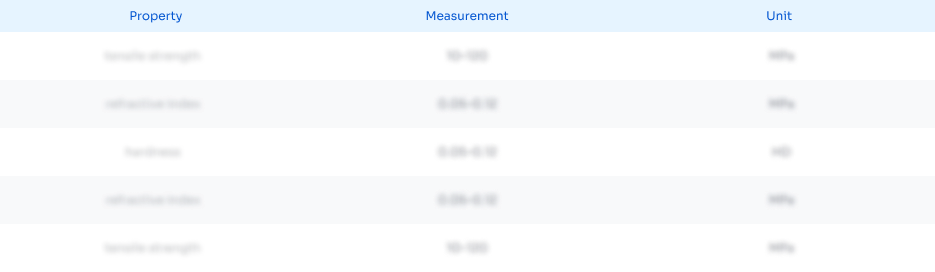
Abstract
Description
Claims
Application Information

- Generate Ideas
- Intellectual Property
- Life Sciences
- Materials
- Tech Scout
- Unparalleled Data Quality
- Higher Quality Content
- 60% Fewer Hallucinations
Browse by: Latest US Patents, China's latest patents, Technical Efficacy Thesaurus, Application Domain, Technology Topic, Popular Technical Reports.
© 2025 PatSnap. All rights reserved.Legal|Privacy policy|Modern Slavery Act Transparency Statement|Sitemap|About US| Contact US: help@patsnap.com