Waste heat recycling system of oil injection screw air compressor
A waste heat recovery system and air compressor technology, applied in mechanical equipment, machines/engines, liquid fuel engines, etc., can solve problems such as large pressure loss and leakage, and achieve the effect of improving reliability
- Summary
- Abstract
- Description
- Claims
- Application Information
AI Technical Summary
Problems solved by technology
Method used
Image
Examples
Embodiment Construction
[0013] The present invention will be described in detail below in conjunction with the accompanying drawings and specific embodiments.
[0014] The waste heat recovery system of the oil-injected screw air compressor of the present invention, such as figure 1 As shown, it includes oil cooling system 1 and heat recovery system 2.
[0015] The oil cooling system 1 includes a cooling tower 3 and a first plate heat exchanger 5, and the first plate heat exchanger 5 is connected to the cooling tower 3 through pipelines. A water inlet pipe 23 is arranged between the cooling tower 3 and the water inlet of the first plate heat exchanger 5, and a second flow control valve 8, a third solenoid valve 14 and a first check valve 9 are arranged in sequence on the water inlet pipe; The water outlet of the plate heat exchanger 5 is connected to the cooling tower 3 through a first water outlet pipe 27; the oil inlet of the first plate heat exchanger 5 is connected with a first oil inlet pipe 21,...
PUM
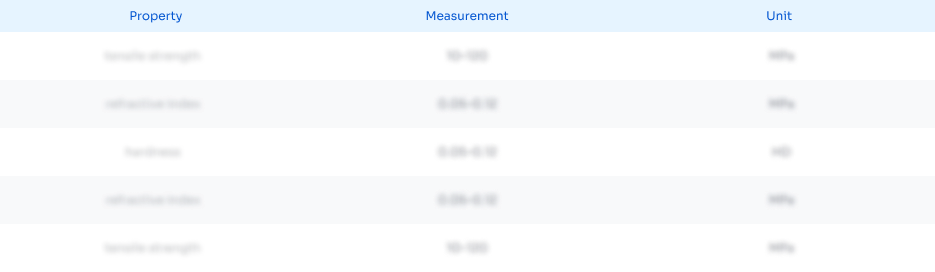
Abstract
Description
Claims
Application Information

- R&D Engineer
- R&D Manager
- IP Professional
- Industry Leading Data Capabilities
- Powerful AI technology
- Patent DNA Extraction
Browse by: Latest US Patents, China's latest patents, Technical Efficacy Thesaurus, Application Domain, Technology Topic, Popular Technical Reports.
© 2024 PatSnap. All rights reserved.Legal|Privacy policy|Modern Slavery Act Transparency Statement|Sitemap|About US| Contact US: help@patsnap.com