Material used for mould, mould and mould preparation method
A mold and mold core technology, applied in the field of molds, can solve the problems affecting the development and application of superplastic molding technology, long mold production cycle, increased investment, etc., to achieve the effect of improving strength, reducing mold sticking, and preventing powder segregation.
- Summary
- Abstract
- Description
- Claims
- Application Information
AI Technical Summary
Problems solved by technology
Method used
Image
Examples
Embodiment 1
[0035] figure 1 Shown is the structural representation of the lower mold of a kind of mold that utilizes the material for mold preparation of the present invention, in the figure, mold core 2 is built-in and installed in the mold case 1, and the mold core 2 is provided with the mold of predetermined shape Cavity 3, the mold cavity 3 is used to accommodate the raw material and shape the raw material.
Embodiment 2
[0037] figure 2 Shown is the structural representation of another kind of mold that utilizes the material for mold preparation of the present invention, in the figure, the structure of mold is eight petals, and 1 is pressing plate, and 2 is heater, and 3 is mold core, and 4 is The mold end screw cap, 5 is the mold end gland, 6 is the raw material, 7 is the air inlet, 8 is the jacket, 9 is the heating jacket, and 10 is the base. Among them, the eight-petal mold is sealed by the jacket 8 to form a mold cavity. The mold can adopt inflation superplastic molding technology. When working, the heater 2 heats the mold core 3 and puts in the raw material 6 to start molding. After the molding is completed, the jacket 8 is released, and the eight-petal mold is separated, and the molded workpiece can be taken out.
[0038] The preparation material of the mold core of the mold shown in embodiment 1 and embodiment 2 can be at least one in pottery, gypsum and cement, in addition, can also ...
Embodiment 3
[0040] First sieve all the materials to separate the particles, and then formulate the mineral base and binder according to the following formula:
[0041] Mix black silicon carbide and other ingredients (including 44.9% by weight of alumina and 0.1% by weight of graphite) at a ratio of 1:1 (the ratio is calculated by weight, the same below) to form a mineral substrate; 60:15:10:5 : Mix alumina, water, fly ash, silica, hydraulic cement, boric acid and borax in a ratio of 6:1:3 to form a binder (water must be added first, and each ingredient is added one by one, and constantly stirred carefully) ; Then mix the mineral base, binder and steel fiber in a ratio of 56:4:40, pour it into the steel mold after mixing, and prevent air bubbles when pouring the mold. After pouring the mold, use a press to compact it with a pressure of 10 tons, and after holding the pressure for 5 minutes, the mold is demoulded to generate a blank. Allow the blank to fix in air for 2 hours. Then carry ou...
PUM
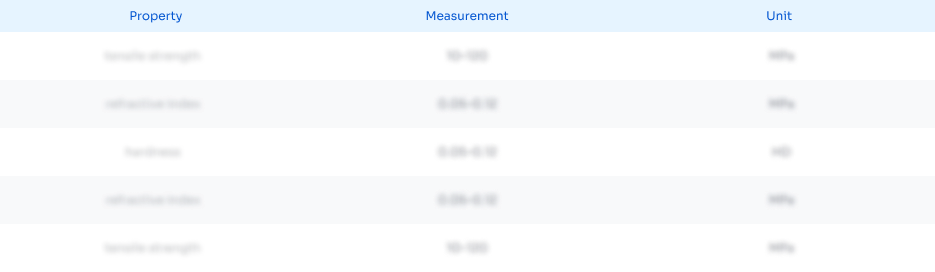
Abstract
Description
Claims
Application Information

- R&D
- Intellectual Property
- Life Sciences
- Materials
- Tech Scout
- Unparalleled Data Quality
- Higher Quality Content
- 60% Fewer Hallucinations
Browse by: Latest US Patents, China's latest patents, Technical Efficacy Thesaurus, Application Domain, Technology Topic, Popular Technical Reports.
© 2025 PatSnap. All rights reserved.Legal|Privacy policy|Modern Slavery Act Transparency Statement|Sitemap|About US| Contact US: help@patsnap.com