Shuttle kiln for sintering ceramic porous body
A porous body, shuttle kiln technology, applied in the shuttle kiln field, can solve the problem of inability to guarantee the oxygen concentration, and achieve the effects of shortening the firing time, increasing the operating cost, and reducing the temperature difference
- Summary
- Abstract
- Description
- Claims
- Application Information
AI Technical Summary
Problems solved by technology
Method used
Image
Examples
Embodiment Construction
[0031] Preferred embodiments of the present invention will be described below. In this embodiment, the object to be fired is a ceramic honeycomb structure containing an organic binder ceramic porous body. The unfired ceramic porous body is loaded into the furnace by the kiln car, the organic binder is evaporated at about 200°C, and then the temperature is raised to about 1500°C for firing.
[0032] figure 1 Among them, 1 is the furnace body of the shuttle kiln. figure 1 In order to simplify the drawings, it is shown that there are three kiln cars 20 in the furnace. In fact, the furnace body 1 can extend to the left and right of the drawing, open the entrance door 21, and load multiple kiln cars into the furnace 1 for firing. . A gas flow path 2 is formed on the bottom surface of each kiln car 20 . In addition, a gas suction path 4 including a gas suction port 3 is provided at a position corresponding to the gas flow path 2 at the bottom of the kiln car. As mentioned above...
PUM
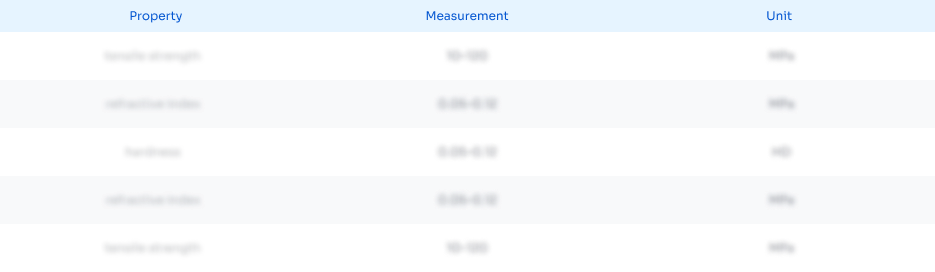
Abstract
Description
Claims
Application Information

- R&D
- Intellectual Property
- Life Sciences
- Materials
- Tech Scout
- Unparalleled Data Quality
- Higher Quality Content
- 60% Fewer Hallucinations
Browse by: Latest US Patents, China's latest patents, Technical Efficacy Thesaurus, Application Domain, Technology Topic, Popular Technical Reports.
© 2025 PatSnap. All rights reserved.Legal|Privacy policy|Modern Slavery Act Transparency Statement|Sitemap|About US| Contact US: help@patsnap.com