Optical fiber
A technology of optical fiber core and core wire, applied in the direction of glass optical fiber, cladding optical fiber, light guide, etc., can solve the problem of increased transmission loss of optical fiber, and achieve the effect that the transmission loss is not easy to increase
- Summary
- Abstract
- Description
- Claims
- Application Information
AI Technical Summary
Problems solved by technology
Method used
Image
Examples
Embodiment )
[0047] Hereinafter, examples of the optical fiber core wires described in the above embodiments will be described.
[0048] In the above-mentioned configuration of the optical fiber core wire 1, an optical fiber core wire 1 with different Young's modulus of the first coating layer 31 and the dissolution rate of the coating resin 3 was produced, and the presence of voids, solvent resistance, and microbending resistance were investigated. characteristic.
[0049] In the manufacture of the sample fiber core wire, as the glass optical fiber 2, the outer diameter (diameter) of about For a 125 μm glass optical fiber, a first coating layer 31 is formed on the outer circumference, and a second coating layer 32 is further formed on the outer circumference, to produce an optical fiber core wire 1. The outer diameter of the first coating layer 31 is 195 μm, and the outer diameter of the second coating layer 32 is 245 μm. These values are examples and can be changed as appropriate.
[0050]...
Embodiment 1
[0070] In Example 1 (Sample No. 2), the first coating layer 31 and the second coating layer 32 use a urethane acrylate ultraviolet curable resin, and each of the first coating layer 31 and the second coating layer 32 The Young's modulus, the dissolution rate of the coating resin 3, the molecular weight of the oligomer, the type of diluting monomer, the ratio of the chain transfer agent, etc., were adjusted to adjust the Young's modulus PY of the first coating layer 31 to 0.14 MPa , The elution rate E when the coating resin 3 is immersed in 60°C warm water for 168 hours is adjusted to 2.4% by mass. In addition, 168 hours are used because the elution from the coating resin is substantially saturated by 168 hours.
Embodiment 2
[0071] In Example 2 (Sample No. 3), the Young’s modulus PY of the first coating layer 31 was adjusted to 0.20 MPa in addition to adjusting the molecular weight of the oligomer, the type of diluting monomer, the ratio of the chain transfer agent, etc., and the coating The resin 3 was the same as in Example 1 above except that the elution rate E when immersed in 60°C warm water for 168 hours was adjusted to 1.8% by mass.
PUM
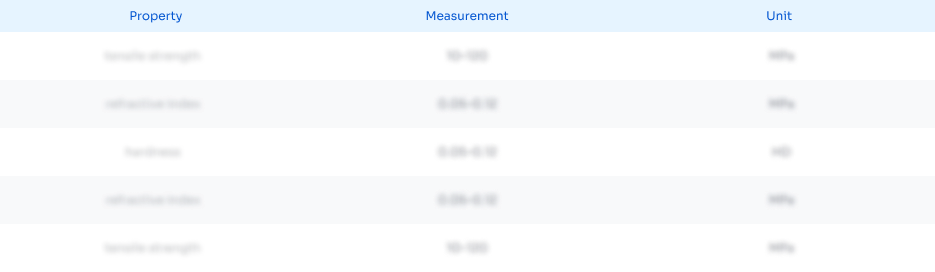
Abstract
Description
Claims
Application Information

- Generate Ideas
- Intellectual Property
- Life Sciences
- Materials
- Tech Scout
- Unparalleled Data Quality
- Higher Quality Content
- 60% Fewer Hallucinations
Browse by: Latest US Patents, China's latest patents, Technical Efficacy Thesaurus, Application Domain, Technology Topic, Popular Technical Reports.
© 2025 PatSnap. All rights reserved.Legal|Privacy policy|Modern Slavery Act Transparency Statement|Sitemap|About US| Contact US: help@patsnap.com