Imaging and temperature measuring device for bogie and underframe of running train
A bogie and vehicle technology, which is applied in transportation and packaging, railway vehicle shape measuring devices, railway car body parts, etc., can solve the problems of train operation safety hazards, failure to alarm, high false alarm rate, etc., and achieve accurate axle temperature alarm rate The effects of improving performance, avoiding economic losses, and eliminating potential safety hazards
- Summary
- Abstract
- Description
- Claims
- Application Information
AI Technical Summary
Problems solved by technology
Method used
Image
Examples
Embodiment
[0017] figure 1 It is shown that a specific embodiment of the present invention is a bogie and underframe imaging and temperature measuring device for running trains, which consists of two orbital center array focal plane infrared thermal imaging sensors 3a installed on the orbital center , a trackside array focal plane infrared thermal imaging sensor 3b is installed on both sides of the track; two track center visible light imagers 4a are installed on the track center, and a track side visible light imager 4b is installed on both sides of the track;
[0018] The track center array focal plane infrared thermal imaging sensor 3a, the track side array focal plane infrared thermal imaging sensor 3b, the track center visible light imager 4a and the track side visible light imager 4b are all connected to the industrial computer 2 on the track side.
[0019] In this example, the superposition of the field of view α1 of the two orbital center array focal plane infrared thermal imagin...
PUM
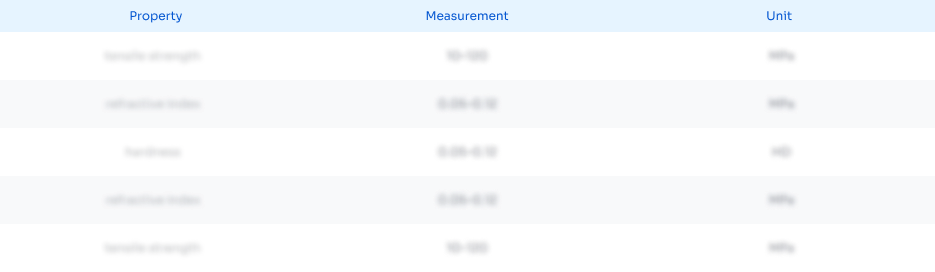
Abstract
Description
Claims
Application Information

- R&D
- Intellectual Property
- Life Sciences
- Materials
- Tech Scout
- Unparalleled Data Quality
- Higher Quality Content
- 60% Fewer Hallucinations
Browse by: Latest US Patents, China's latest patents, Technical Efficacy Thesaurus, Application Domain, Technology Topic, Popular Technical Reports.
© 2025 PatSnap. All rights reserved.Legal|Privacy policy|Modern Slavery Act Transparency Statement|Sitemap|About US| Contact US: help@patsnap.com