Sweater fleece falling prevention technology
A process and anti-shedding technology, which is applied in the field of sweater woolen technology, can solve the problems of poor thermal insulation performance, messy fibers, uneven length, etc., and achieve the effects of strong thermal insulation performance, preventing fluff from shedding, and not easily deformed.
- Summary
- Abstract
- Description
- Claims
- Application Information
AI Technical Summary
Problems solved by technology
Method used
Examples
Embodiment 1
[0018] (A) Select raw materials, use 32 cotton as the fabric, and steamed polyester low-stretch yarn as the base material, of which 32-count cotton accounts for 30% by mass, and polyester low-stretch yarn accounts for 70% by mass.
[0019] (B) Use a 30-inch 22-pin single-sided machine for programming.
[0020] (C) Dyeing: In the high-temperature and high-pressure dyeing machine, disperse dyes are used to dye the fabric. When the temperature reaches 60℃, the cloth is fed in, and when the temperature rises to 130℃, it is kept warm. The temperature rise time is 80min, and the heat preservation time is 40min. Cool down to 40℃ for fabric.
[0021] (D) Trimming, rub the dyed cloth with a roller covered with sand skin on the cloth surface to grind a layer of fluff on the cloth surface; use a 24-roller high-speed grabbing machine to grab the bottom surface of the cloth 4 times, control the cloth speed of the hair 20m / min; go through the carding machine to comb the hair, and the cloth speed ...
Embodiment 2
[0024] (A) Select the raw material, use 40 cotton as the fabric, and steamed polyester low-elastic yarn as the base material, of which 40-thread cotton accounts for 40% by mass, and polyester low-elastic yarn accounts for 60% by mass.
[0025] (B) Use 34-inch 20-pin single-sided machine for programming.
[0026] (C) Dyeing: In the high-temperature and high-pressure dyeing machine, disperse dyes are used to dye the fabric. When the temperature reaches 80°C, the cloth is inserted, and when the temperature rises to 140°C, heat preservation is performed. The temperature rise time is 100min, and the heat preservation time is 60min. Cool down to 50°C for cloth.
[0027] (D) Trimming, rub the dyed cloth with a roller covered with sand skin on the cloth surface to grind a layer of fluff on the cloth surface; use a 24-roller high-speed grabbing machine to grab the bottom surface of the cloth 2 times, control the hair grabbing speed of 30m / min; after the carding machine for combing, the cardi...
Embodiment 3
[0030] (A) Select raw materials, use 40 cotton as the fabric, and steamed polyester low-elastic yarn as the base material, of which 40-thread cotton accounts for 35% by mass, and polyester low-elastic yarn accounts for 65% by mass.
[0031] (B) Use a 30-inch 20-pin single-sided machine for programming.
[0032] (C) Dyeing: In the high-temperature and high-pressure dyeing machine, disperse dyes are used to dye the fabric. When the temperature reaches 60°C, the cloth is inserted, and when the temperature rises to 130°C, heat preservation is carried out. The temperature rise time is 70min, and the heat preservation time is 30min. Cool down to 45℃ for cloth.
[0033] (D) Trimming, rub the dyed cloth with a roller covered with sand skin on the cloth surface to grind a layer of fluff on the cloth surface; use a 24-roller high-speed grabbing machine to grab the bottom surface of the cloth 3 times, control the cloth speed of the hair to 25m / min; go through the carding machine to comb the ha...
PUM
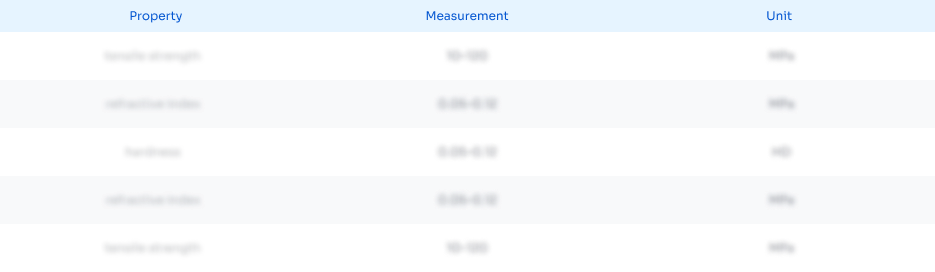
Abstract
Description
Claims
Application Information

- R&D Engineer
- R&D Manager
- IP Professional
- Industry Leading Data Capabilities
- Powerful AI technology
- Patent DNA Extraction
Browse by: Latest US Patents, China's latest patents, Technical Efficacy Thesaurus, Application Domain, Technology Topic, Popular Technical Reports.
© 2024 PatSnap. All rights reserved.Legal|Privacy policy|Modern Slavery Act Transparency Statement|Sitemap|About US| Contact US: help@patsnap.com