Gripping mechanical fingers with specific motion trajectory
A technology of movement trajectory and mechanical fingers, which is applied in the field of manufacturing, can solve the problems of complex structure and single movement of mechanical fingers, and achieve the effect of simple structure, simple operation and simple mechanism structure
- Summary
- Abstract
- Description
- Claims
- Application Information
AI Technical Summary
Problems solved by technology
Method used
Image
Examples
Embodiment Construction
[0014] In order to make the above-mentioned features and advantages of the present invention more comprehensible, the following specific embodiments are described in detail with reference to the accompanying drawings.
[0015] refer to Figure 1 to Figure 5 , the present invention relates to a clamping mechanical finger with a specific movement trajectory, including at least one pair of clamping plates 1 for clamping materials and a bottom plate 2 for installing the clamping plates 1, and at least one pair of symmetrical The set of guide grooves 3 is arranged. The guide groove group 3 is composed of two independent upper guide grooves 3-1 and lower guide grooves 3-2. The splint 1 is composed of the upper longitudinal section 1-1 and the lower Clamping section 1-2, the upper and lower parts of the longitudinal section 1-1 of the splint are respectively provided with rollers 4 installed in the upper guide groove 3-1 and the lower guide groove 3-2, so as to realize rolling connec...
PUM
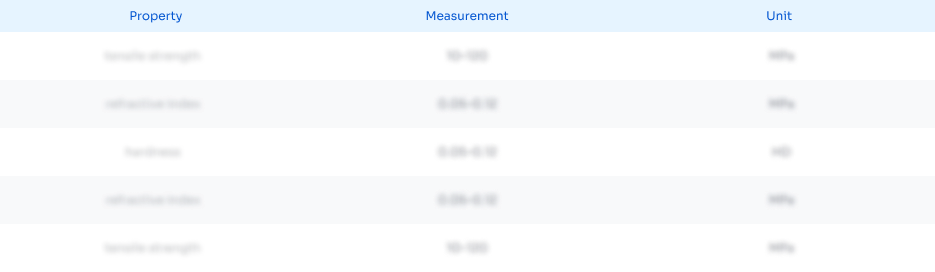
Abstract
Description
Claims
Application Information

- Generate Ideas
- Intellectual Property
- Life Sciences
- Materials
- Tech Scout
- Unparalleled Data Quality
- Higher Quality Content
- 60% Fewer Hallucinations
Browse by: Latest US Patents, China's latest patents, Technical Efficacy Thesaurus, Application Domain, Technology Topic, Popular Technical Reports.
© 2025 PatSnap. All rights reserved.Legal|Privacy policy|Modern Slavery Act Transparency Statement|Sitemap|About US| Contact US: help@patsnap.com