Full-automatic plate plastics sucking moulding machine
A blister molding machine, fully automatic technology, applied in the field of improved invention, can solve the problems of low production efficiency, high manual operation cost, large power consumption, etc., and achieve the effect of improving production efficiency, reducing production cost and speeding up replacement
- Summary
- Abstract
- Description
- Claims
- Application Information
AI Technical Summary
Problems solved by technology
Method used
Image
Examples
Embodiment Construction
[0020] With reference to the accompanying drawings, this kind of fully automatic sheet material blister forming machine includes a frame 9, a forming device, a heating device 20, a conveying device and a material table 21, and the forming device has two groups, namely, a forming device-1 and a forming device 2. The material platform 21 also has two groups, and the two groups of material platforms are respectively arranged in front of the two groups of forming devices 1, 2, so that two groups of different products can be produced at the same time, such as some products with box lids. Can be done by one machine. The frame 9 includes a reserved heating position 24, which is arranged on the side of the forming device 1, 2, and the heating device 20 is in the reserved heating position 24 when it is not working. Described frame 9 is provided with first guide rail 37 and second guide rail, and described heating device 20 is connected with power source, and power source is cylinder, a...
PUM
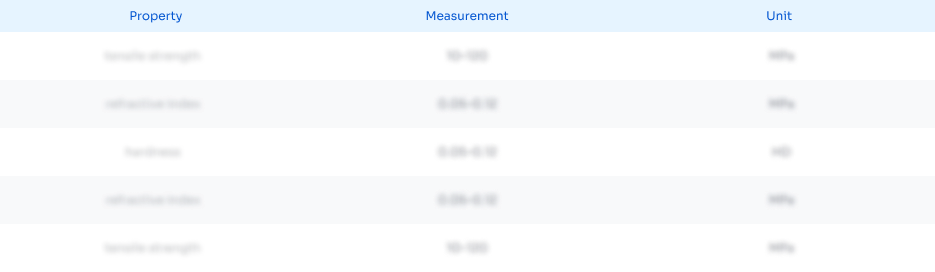
Abstract
Description
Claims
Application Information

- R&D
- Intellectual Property
- Life Sciences
- Materials
- Tech Scout
- Unparalleled Data Quality
- Higher Quality Content
- 60% Fewer Hallucinations
Browse by: Latest US Patents, China's latest patents, Technical Efficacy Thesaurus, Application Domain, Technology Topic, Popular Technical Reports.
© 2025 PatSnap. All rights reserved.Legal|Privacy policy|Modern Slavery Act Transparency Statement|Sitemap|About US| Contact US: help@patsnap.com