A flip-chip process of power semiconductor modules before welding
A power semiconductor, flip-chip technology, applied in semiconductor devices, semiconductor/solid-state device manufacturing, electric solid-state devices, etc., can solve the problems of electrode failure, increased assembly time, low labor productivity, etc., to improve positioning accuracy, improve Good quality and reliability, consistent product performance
- Summary
- Abstract
- Description
- Claims
- Application Information
AI Technical Summary
Problems solved by technology
Method used
Image
Examples
Embodiment Construction
[0028] The following are specific embodiments of the present invention and in conjunction with the accompanying drawings, the technical solutions of the present invention are further described, but the present invention is not limited to these embodiments.
[0029] Such as figure 1 As shown, the flip-chip process of the power semiconductor module before welding, the power semiconductor module includes a base plate 6, an insulating sheet or a DBC substrate 5, a die or chip 4, an internal interconnection electrode 3 and a lead-out electrode 2, the flip-chip process The specific steps are as follows: Step 1, making a bracket 1 that has a mounting groove 1a and supports and fixes the components in the power semiconductor module through the mounting groove 1a; Step 2, placing the lead-out electrode 2 in the mounting groove 1a of the bracket 1 and For positioning and fixing, the lead-out electrode 2 includes a lead-out pole 2a for connecting to an external circuit and a welding pol...
PUM
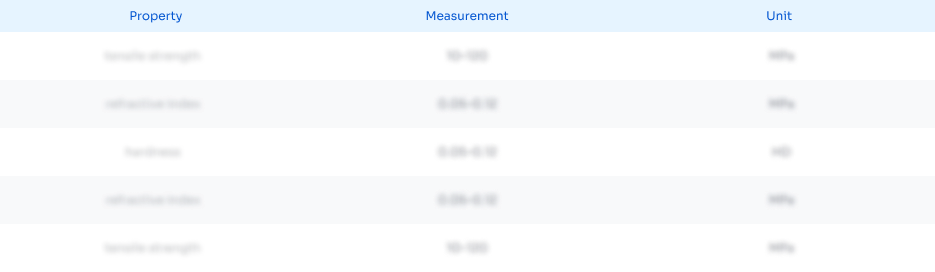
Abstract
Description
Claims
Application Information

- R&D
- Intellectual Property
- Life Sciences
- Materials
- Tech Scout
- Unparalleled Data Quality
- Higher Quality Content
- 60% Fewer Hallucinations
Browse by: Latest US Patents, China's latest patents, Technical Efficacy Thesaurus, Application Domain, Technology Topic, Popular Technical Reports.
© 2025 PatSnap. All rights reserved.Legal|Privacy policy|Modern Slavery Act Transparency Statement|Sitemap|About US| Contact US: help@patsnap.com