Self-lubrication cooled type gear shaper spindle structure
An automatic lubricating and cooling technology, used in metal processing machinery parts, maintenance and safety accessories, metal processing equipment, etc., can solve the problems of locked spindle sleeve, large force, insufficient lubrication, etc., to prevent spindle wear and tear. , Small thermal deformation, the effect of preventing the spindle from grinding to death
- Summary
- Abstract
- Description
- Claims
- Application Information
AI Technical Summary
Problems solved by technology
Method used
Image
Examples
Embodiment Construction
[0014] The structure of the present invention is as figure 1 As shown in -3, an automatic lubricating and cooling type gear shaper spindle structure, which includes a spindle 4, one end of the spindle is provided with a hanging tool sleeve 6, and the outside of the spindle 4 is provided with a spindle sleeve 3, and the spindle 4 moves up and down inside the spindle sleeve 3 and rotating movement, the main shaft sleeve 3 is embedded in the tool holder body 2, and the upper end of the main shaft sleeve 3 is respectively provided with an oil inlet 1 and an oil outlet 7, and the main shaft sleeve 3 is provided with a spiral oil groove 8, and the outer circle of the main shaft sleeve 3 There are multiple annular cooling grooves 9, and the lower end of the annular cooling grooves 9 communicates with the spiral oil groove 8. The main shaft 4, the main shaft sleeve 3, the tool holder body 2, the oil inlet 1 and the oil outlet 7 form a closed oil circulation system. There is clearance ...
PUM
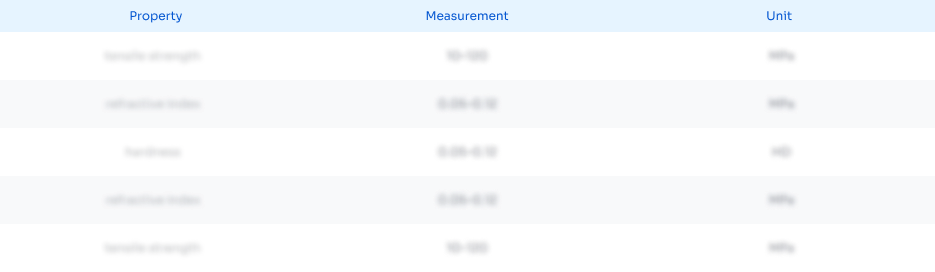
Abstract
Description
Claims
Application Information

- R&D
- Intellectual Property
- Life Sciences
- Materials
- Tech Scout
- Unparalleled Data Quality
- Higher Quality Content
- 60% Fewer Hallucinations
Browse by: Latest US Patents, China's latest patents, Technical Efficacy Thesaurus, Application Domain, Technology Topic, Popular Technical Reports.
© 2025 PatSnap. All rights reserved.Legal|Privacy policy|Modern Slavery Act Transparency Statement|Sitemap|About US| Contact US: help@patsnap.com