Design method for support ribs of ballast slipping plate of cutter head of full face rock tunnel boring machine
A design method and technology of supporting bars, applied in mining equipment, earth-moving drilling, tunnels, etc.
- Summary
- Abstract
- Description
- Claims
- Application Information
AI Technical Summary
Problems solved by technology
Method used
Image
Examples
Embodiment Construction
[0039] The specific implementation of the present invention will be described in detail in conjunction with the accompanying drawings and technical solutions. During the working process of the full-face rock boring machine, the scraper is arranged around the cutter head, and the rock crushed by the hob falls to the bottom of the cutter head by its own weight. When the scraper passes through the bottom of the cutter head, it will scrape up this part of the rock The scraped rocks will fall onto the ballast slide plate, and the rock ballast will gradually overcome the friction between the ballast slide plate and the ballast slide plate during the rotation of the cutter head, and then fall along the ballast slide plate to the belt conveyor for discharge .
[0040] The ballast discharge system of the full-face rock boring machine has an important impact on the overall work efficiency. If the rock ballast cannot be discharged from the cutter head in time, the full-face rock roadhead...
PUM
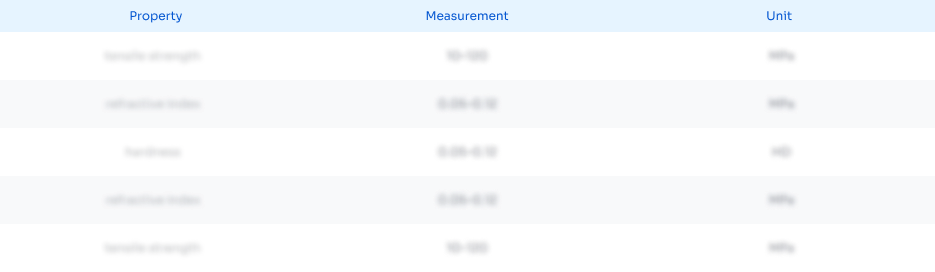
Abstract
Description
Claims
Application Information

- R&D
- Intellectual Property
- Life Sciences
- Materials
- Tech Scout
- Unparalleled Data Quality
- Higher Quality Content
- 60% Fewer Hallucinations
Browse by: Latest US Patents, China's latest patents, Technical Efficacy Thesaurus, Application Domain, Technology Topic, Popular Technical Reports.
© 2025 PatSnap. All rights reserved.Legal|Privacy policy|Modern Slavery Act Transparency Statement|Sitemap|About US| Contact US: help@patsnap.com