Three-freedom-degree and four-freedom-degree parallel mechanism
A degree of freedom, parallel technology, applied in manipulators, program-controlled manipulators, manufacturing tools, etc., can solve the problems of equipment installation and debugging, complex control algorithms of parallel structures, and long time to complete actions, etc., to reduce the constraints of kinematic pairs. , Simple structure, simple debugging effect
- Summary
- Abstract
- Description
- Claims
- Application Information
AI Technical Summary
Problems solved by technology
Method used
Image
Examples
Embodiment 1
[0045] For the three-degree-of-freedom parallel mechanism according to an embodiment of the present invention, please refer to Figure 1 to Figure 3 . A three-degree-of-freedom parallel mechanism includes three support rods 10, three lifting blocks 11, three groups of parallelogram mechanisms, a moving platform 30, and a static platform 12 that can be used or not used according to the installation environment.
[0046] The three support rods 10 are parallel to each other and are respectively arranged on the three corners of the same equilateral triangle, and the three support rods 10 enclose an equilateral triangle cylindrical space. The drawing shows the situation where the static platform 12 is used, and the static platform 12 is an equilateral triangle, and each corner is provided with a support rod 10 , and the support rod 10 is perpendicular to the static platform 12 .
[0047] A lifting block 11 is installed on each support rod 10 , and each lifting block 11 is connecte...
Embodiment 2
[0051] see Figure 4 , the four-degree-of-freedom parallel mechanism in another embodiment of the present invention includes the three-degree-of-freedom parallel mechanism described in Embodiment 1. The difference is that a rotating mechanism is installed on the static platform 12, and the rotating mechanism is used to rotate the processed artifact. “On the static platform 12 ” refers to the connection relationship, not the positional relationship. The rotating mechanism can be located above the static platform 12 or below the static platform 12 . When the static platform 12 was arranged on the lower end of the support rod 10, the turning mechanism was installed above the static platform 12; The rotating mechanism described in this embodiment is a rotating shaft 40, which is connected to the static platform through a universal joint.
Embodiment 3
[0053] In another embodiment of the present invention, the four-degree-of-freedom parallel mechanism includes the three-degree-of-freedom parallel mechanism described in Embodiment 1, but the difference is that a rotating mechanism is installed on the moving platform 30 . “On the moving platform 30 ” refers to the connection relationship, not the positional relationship. The rotating mechanism can be located above the moving platform 30 or below the moving platform 30 . When the static platform 12 was arranged on the lower end of the support rod 10, the turning mechanism was installed below the moving platform 30; The rotating mechanism described in this embodiment is a rotating shaft, which is connected to the moving platform through a universal joint. Alternatively, the rotating mechanism is a motor, which is connected to the moving platform through a bearing.
PUM
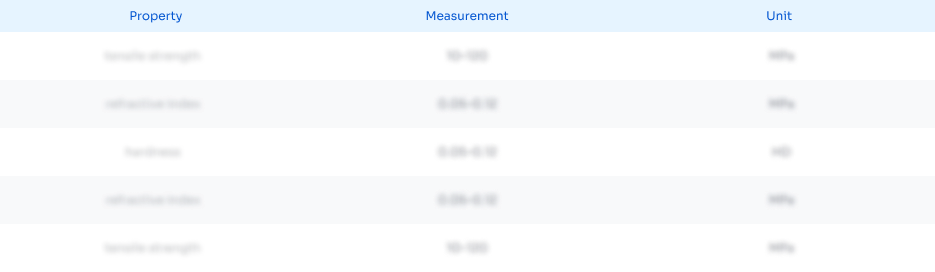
Abstract
Description
Claims
Application Information

- R&D
- Intellectual Property
- Life Sciences
- Materials
- Tech Scout
- Unparalleled Data Quality
- Higher Quality Content
- 60% Fewer Hallucinations
Browse by: Latest US Patents, China's latest patents, Technical Efficacy Thesaurus, Application Domain, Technology Topic, Popular Technical Reports.
© 2025 PatSnap. All rights reserved.Legal|Privacy policy|Modern Slavery Act Transparency Statement|Sitemap|About US| Contact US: help@patsnap.com