Soft measurement method and system of tool nose point displacement mobility of machining center
A technology of displacement admittance and machining center, which is used in measuring devices, measuring mechanical impedance, measuring ultrasonic/sonic/infrasonic waves, etc., and can solve the problem of difficult and accurate implementation of rotation angles.
- Summary
- Abstract
- Description
- Claims
- Application Information
AI Technical Summary
Problems solved by technology
Method used
Image
Examples
Embodiment Construction
[0064] The specific implementation manners of the present invention will be described in detail below in conjunction with the accompanying drawings.
[0065] In this embodiment, the soft measuring system of the tool tip point displacement admittance of the machining center includes a tool, a test rod 7, an acceleration sensor 9, a force hammer 8, a data acquisition card 10 and a computer 11;
[0066] The test rod 7 or the tool is installed on the tool handle 4 of the machining center, the tool handle 4 is installed on the spindle 3 of the machining center, the acceleration sensor 9 is pasted on the end side of the test rod 7 or the end side of the tool, the signal output terminal of the force hammer 8, the acceleration The output terminals of the sensors 9 are all connected to the computer 11 through the data acquisition card 10 .
[0067] The force hammer 8 is used to excite the front end of the tool or the front end of the test rod 7 .
[0068] Test rod 7 is a standard shor...
PUM
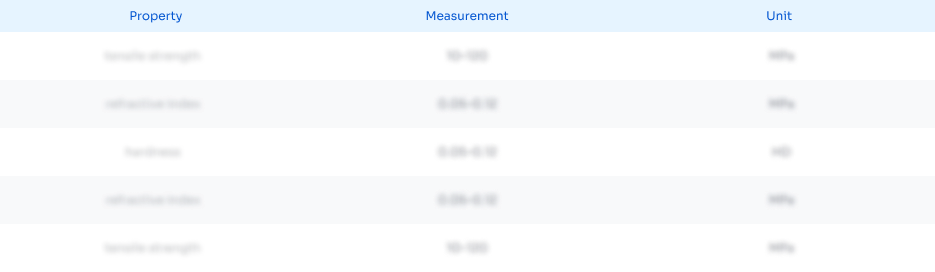
Abstract
Description
Claims
Application Information

- R&D
- Intellectual Property
- Life Sciences
- Materials
- Tech Scout
- Unparalleled Data Quality
- Higher Quality Content
- 60% Fewer Hallucinations
Browse by: Latest US Patents, China's latest patents, Technical Efficacy Thesaurus, Application Domain, Technology Topic, Popular Technical Reports.
© 2025 PatSnap. All rights reserved.Legal|Privacy policy|Modern Slavery Act Transparency Statement|Sitemap|About US| Contact US: help@patsnap.com