Method for prefabricated assembly of middle-divided sections of large-sized capping beam and assembly structure of middle-divided sections of large-sized capping beam
A prefabricated assembly and segmented technology, which is applied to bridges, bridge parts, bridge construction, etc., can solve the problems of high construction requirements, limited ground traffic, and long erection period, so as to shorten the construction period, facilitate on-site construction, and reduce construction costs. effect of difficulty
- Summary
- Abstract
- Description
- Claims
- Application Information
AI Technical Summary
Problems solved by technology
Method used
Image
Examples
Embodiment 1
[0024] figure 1 Schematic flow diagram of the segmental prefabrication assembly method for large cap beams. This example proposes a segmental prefabricated assembly method for a large-scale cap girder, so as to realize the successful hoisting of a large-scale cap girder exceeding 400 tons on two bridge piers, such as figure 1 As shown, it specifically includes the following steps:
[0025] Step S1: According to design requirements, divide the cover beam from the middle into two prefabricated sections 1 for prefabrication. Both prefabricated sections 1 are provided with transverse sleeves for piercing prestressed tendons 5 and for piercing The longitudinal casing of the connecting piece 3 connected to the pier 2; for example, the connecting piece 3 in this embodiment is JL32 finish-rolled rebar.
[0026] Step S2: Combine Figure 2-4 As shown, the prefabricated segment 1 is hoisted to the pier 2 by a crane, and the connecting piece 3 is pierced in the longitudinal casing to c...
Embodiment 2
[0031] Figure 5 Schematic diagram for the application of segmental prefabricated assembly structures in large cap beams. In this embodiment, a segmental prefabricated assembly structure in a large cap beam can be built according to the construction steps of the first embodiment, such as Figure 5 As shown, the assembled structure includes two prefabricated segments 1 and a cast-in-place segment 6, the two pre-fabricated segments 1 are connected through the cast-in-place segment 6, and prestressed tendons are arranged between the two prefabricated segments 1 and the cast-in-place segment 6 5.
[0032] As a further specific implementation of this embodiment, as Figure 5 and Figure 6 As shown, the two prefabricated sections 1 are provided with transverse casings for piercing the prestressing tendons 5, and the prefabricated sections 1 are provided with longitudinal casings for piercing the connectors 3 connected with the pier. The transverse casing and the longitudinal cas...
PUM
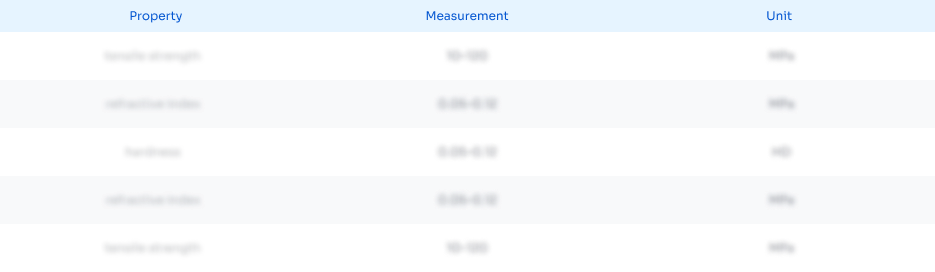
Abstract
Description
Claims
Application Information

- R&D
- Intellectual Property
- Life Sciences
- Materials
- Tech Scout
- Unparalleled Data Quality
- Higher Quality Content
- 60% Fewer Hallucinations
Browse by: Latest US Patents, China's latest patents, Technical Efficacy Thesaurus, Application Domain, Technology Topic, Popular Technical Reports.
© 2025 PatSnap. All rights reserved.Legal|Privacy policy|Modern Slavery Act Transparency Statement|Sitemap|About US| Contact US: help@patsnap.com