Hydrogen peroxide-hydrochloric acid oxidation and desulfurization method
A technology for oxidative desulfurization and hydrogen peroxide, applied in the field of hydrogen peroxide-hydrochloric acid oxidative desulfurization, can solve the problems of difficult large-scale application and high production cost, and achieve the effects of economical reaction, low price and mild reaction conditions
- Summary
- Abstract
- Description
- Claims
- Application Information
AI Technical Summary
Problems solved by technology
Method used
Examples
Embodiment 1
[0027] Example 1. Simulating the desulfurization effect of dibenzothiophene in fuel oil
[0028] Follow the steps below to desulfurize dibenzothiophene n-octane simulated fuel;
[0029] 1. Take 5.00 ml of n-octane containing 2.50 mM dibenzothiophene, add 5.00 ml of 37% (W / W) hydrogen peroxide, add 5.00 ml of 1M hydrochloric acid solution, add 0.2 ml of ethanol, seal it in the reaction kettle, and the reaction temperature is 50°C, vigorously stirred for 2 hours.
[0030] 2. After the simulated fuel oil has stood still for 10 minutes, take 10ul each of the simulated fuel oil and n-octane containing 2.50 mM dibenzothiophene, dissolve and mix with 3.00ml ethanol, measure the absorbance at 236nm, and calculate the desulfurization rate of dibenzothiophene to be 75.0 %.
Embodiment 2
[0031] Example 2: Desulfurization effect of 4,6-dibenzothiophene in simulated fuel
[0032] Follow the steps below to desulfurize 4,6-dibenzothiophene n-octane simulated fuel.
[0033] 1. Take 5.00 ml of n-octane containing 2.50 mM 4,6-dibenzothiophene, add 5.00 ml of 37% (W / W) hydrogen peroxide, add 5.00 ml of 1M hydrochloric acid solution, add 0.2 ml of ethanol, and seal it in the reaction kettle , the reaction temperature was 50° C., and vigorously stirred for 4 hours.
[0034] 2. After the simulated fuel was left standing for 10 minutes, take 10ul each of the treated simulated fuel and n-octane containing 2.50 mM 4,6-dibenzothiophene, dissolve and mix with 3.00ml n-octane, measure the absorbance at 241nm, and calculate 4, The desulfurization rate of 6-dibenzothiophene is over 70.0%.
Embodiment 3
[0035] Example 3: Desulfurization effect of benzothiophene in simulated fuel
[0036] Follow the steps below to desulfurize benzothiophene n-octane simulated fuel.
[0037] 1. Take 5.00 ml of n-octane containing 2.50 mM benzothiophene, add 5.00 ml of 37% (W / W) hydrogen peroxide, add 5.00 ml of 1M hydrochloric acid solution, add 0.2 ml of ethanol, seal it in the reaction kettle, and the reaction temperature is 50 °C, vigorously stirred for 2 hours.
[0038] 2. After the simulated fuel was left standing for 10 minutes, take 10ul each of the treated simulated fuel and n-octane containing 2.50 mM benzothiophene, dissolve and mix with 3.00ml ethanol, measure the absorbance at 226nm, and calculate the desulfurization rate of benzothiophene to be over 65.0% .
PUM
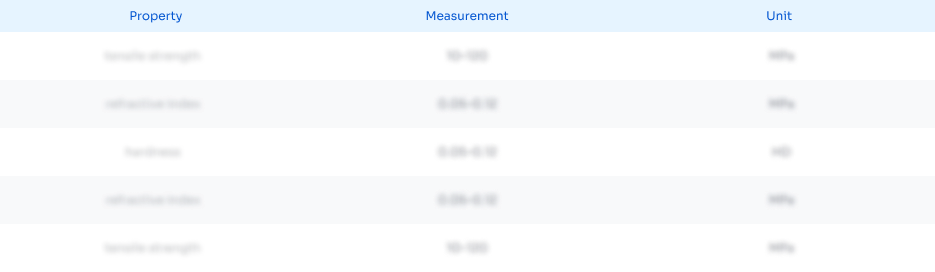
Abstract
Description
Claims
Application Information

- Generate Ideas
- Intellectual Property
- Life Sciences
- Materials
- Tech Scout
- Unparalleled Data Quality
- Higher Quality Content
- 60% Fewer Hallucinations
Browse by: Latest US Patents, China's latest patents, Technical Efficacy Thesaurus, Application Domain, Technology Topic, Popular Technical Reports.
© 2025 PatSnap. All rights reserved.Legal|Privacy policy|Modern Slavery Act Transparency Statement|Sitemap|About US| Contact US: help@patsnap.com