Load-sharing piezoelectric multi-dimensional force measuring device and method for manufacturing the same
A manufacturing method and technology of measuring devices, which are applied in the field of 10,000 ox level test devices, can solve the problems that cannot be applied, and the measuring range in two tangential directions cannot reach the 10,000 ox level, so as to reduce assembly technical requirements, broaden the measurement range, and structure simple effect
- Summary
- Abstract
- Description
- Claims
- Application Information
AI Technical Summary
Problems solved by technology
Method used
Image
Examples
Embodiment 1
[0027] Embodiment 1, the outer diameter of getting expansion pin is respectively 10mm and 12mm, and the load sharing effect obtained is as follows Figure 5 , Figure 6 , Figure 7 shown. It can be seen that the load sharing in the tangential Y direction is 80% and 85% when the expansion pin is 10mm and 12mm, the load sharing in the tangential X direction is 60% and 70% when the expansion pin is 10mm and 12mm, and the normal Z direction is Forward load sharing is limited to only 10%. Moreover, the linearity of each output after load sharing is very good.
[0028] The load-sharing large-range piezoelectric multi-dimensional force measuring device is simple in manufacturing process, easy to use, easy to package, and small in size. For the six-dimensional force testing device using multiple sets of three-dimensional force sensors, this method can be used to share the load of each sensor, which is convenient for making a large-range six-dimensional force testing device, which ...
PUM
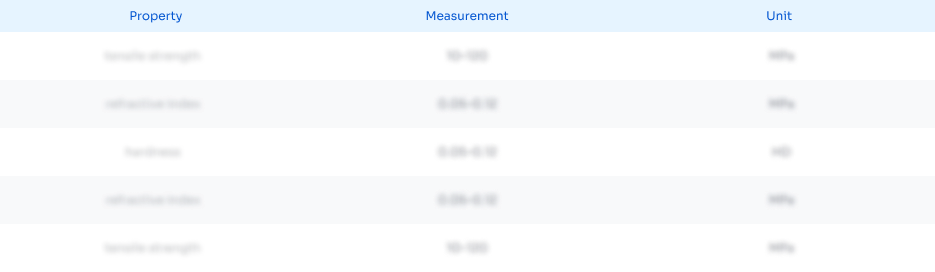
Abstract
Description
Claims
Application Information

- R&D Engineer
- R&D Manager
- IP Professional
- Industry Leading Data Capabilities
- Powerful AI technology
- Patent DNA Extraction
Browse by: Latest US Patents, China's latest patents, Technical Efficacy Thesaurus, Application Domain, Technology Topic, Popular Technical Reports.
© 2024 PatSnap. All rights reserved.Legal|Privacy policy|Modern Slavery Act Transparency Statement|Sitemap|About US| Contact US: help@patsnap.com