Printing roller for temperature-adjustable type double-loop multi-channel wide-range film pressing machine
An adjustable, double-loop technology, used in general parts of printing machinery, printing machines, printing and other directions, can solve the problems of inability to flexibly change the working area, high degree of temperature field coupling, and inability to flexibly change the size, so as to avoid micro mutual The effect of leakage, high product precision, good isolation effect
- Summary
- Abstract
- Description
- Claims
- Application Information
AI Technical Summary
Problems solved by technology
Method used
Image
Examples
Embodiment Construction
[0025] The present invention will be further specifically described below in conjunction with the embodiments and the accompanying drawings.
[0026] Such as Figure 1-4 As shown, the temperature-adjustable double-circuit multi-channel wide-width film press roller includes a main shaft body 5, an oil shaft 1, a water shaft 7, an oil channel 8, a water channel 3, an oil outlet pipe, and a water inlet pipe , the water outlet pipe, the first isolation plate 9 and the second isolation plate 10, the main shaft body 5 is a hollow structure, including the inner cavity 2 and the shaft wall 12; the oil channel 8 and the water channel 3 are arranged on the main shaft body 5 In the shaft wall 12 of the shaft body, the oil shaft 1 and the water shaft 7 are symmetrically arranged at both ends of the main shaft body 5 respectively, the oil shaft 1 communicates with the inner cavity 2 of the main shaft body 5, and the inner side of the shaft wall 12 of the main shaft body 5 There is a commu...
PUM
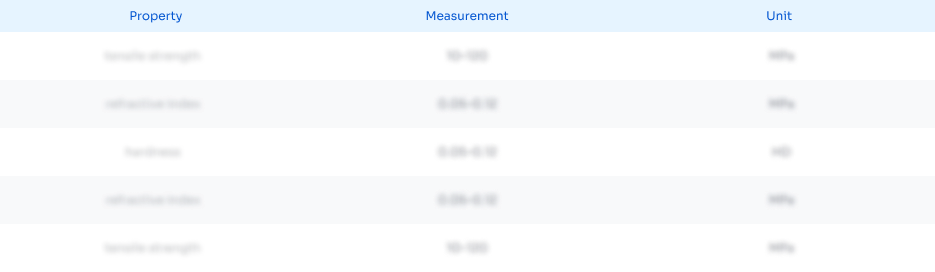
Abstract
Description
Claims
Application Information

- R&D
- Intellectual Property
- Life Sciences
- Materials
- Tech Scout
- Unparalleled Data Quality
- Higher Quality Content
- 60% Fewer Hallucinations
Browse by: Latest US Patents, China's latest patents, Technical Efficacy Thesaurus, Application Domain, Technology Topic, Popular Technical Reports.
© 2025 PatSnap. All rights reserved.Legal|Privacy policy|Modern Slavery Act Transparency Statement|Sitemap|About US| Contact US: help@patsnap.com