Dust-removal mercury-removal filter bag for bag-type dust remover and preparation method of filter bag
A bag filter and mercury removal technology, applied in chemical instruments and methods, separation methods, dispersed particle filtration, etc., can solve the problems of affecting the quality of fly ash, affecting working performance, low adsorption capacity, etc., to meet the requirements of flue gas mercury removal. Requirement, low investment and operating costs, and simple preparation process
- Summary
- Abstract
- Description
- Claims
- Application Information
AI Technical Summary
Problems solved by technology
Method used
Examples
Embodiment 1
[0024] Preparation of Mn(5)-CoO(1)-PSA filter bag: the active component MnO 2 After the precursor manganese nitrate of manganese nitrate is stirred and dissolved in water, the precursor cobalt nitrate of the active component CoO is added, and the mixture is evenly stirred to obtain a mixed solution. In the composite solution, MnO 2 The mass ratio to CoO was 5:1, and the filter bag made of polysulfonamide fiber (PSA) was immersed in the mixed solution for multiple impregnations of equal volume, and left to stand for 24 hours; the solution was evaporated to dryness at 60°C to 100°C, Place in a clean drying oven at 100°C until completely dry; place the filter bag in a muffle furnace, decompose cobalt nitrate and manganese nitrate for 4 hours at 250°C. After the decomposition is completed, stop the heating of the muffle furnace, let it drop to normal temperature naturally, and make a dust removal and mercury removal filter bag, in which MnO 2 The loading of CoO is 5 wt%, the load...
Embodiment 2
[0026] Preparation of Mn(5)-CoO(3)-PSA filter bag: the active component MnO 2 After the precursor manganese nitrate of manganese nitrate is stirred and dissolved in water, the precursor cobalt nitrate of the active component CoO is added, and the mixture is evenly stirred to obtain a mixed solution. In the composite solution, MnO 2 The mass ratio to CoO was 5:3, and the filter bag made of sulfonamide fiber (PSA) was immersed in the mixed solution for multiple impregnations of equal volume, and stood for 24 hours; at 60 o Evaporate the solution at C ~ 100 ℃, put it in a clean drying oven at 100 ℃ until completely dry; put the filter bag in a muffle furnace, decompose cobalt nitrate and manganese nitrate at 250 ℃ for 4 hours. After the decomposition is completed, stop the heating of the muffle furnace, let it drop to normal temperature naturally, and make a dust removal and mercury removal filter bag, in which MnO 2 The loading of CoO is 5 wt%, the loading of CoO is 3 wt%, and ...
Embodiment 3
[0028] Preparation of Mn(5)-CoO(5)-PSA filter bag: the active component MnO 2 After the precursor manganese nitrate of manganese nitrate is stirred and dissolved in water, the precursor cobalt nitrate of the active component CoO is added, and the mixture is evenly stirred to obtain a mixed solution. In the composite solution, MnO 2 The mass ratio to CoO was 5:5, and the filter bag made of polysulfonamide fiber (PSA) was immersed in the mixed solution for multiple impregnations of equal volume, and left to stand for 24 hours; the solution was evaporated to dryness at 60°C-100°C, Place in a clean drying oven at 100°C until completely dry; place the filter bag in a muffle furnace, decompose cobalt nitrate and manganese nitrate for 4 hours at 250°C. After the decomposition is completed, stop the heating of the muffle furnace, let it drop to normal temperature naturally, and make a dust removal and mercury removal filter bag, in which MnO 2 The loading of CoO is 5wt%, the loading ...
PUM
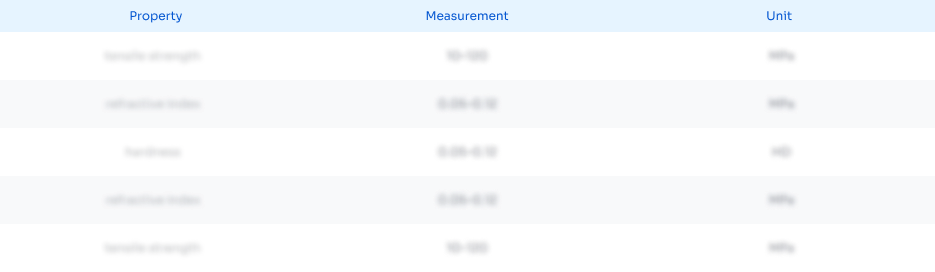
Abstract
Description
Claims
Application Information

- R&D
- Intellectual Property
- Life Sciences
- Materials
- Tech Scout
- Unparalleled Data Quality
- Higher Quality Content
- 60% Fewer Hallucinations
Browse by: Latest US Patents, China's latest patents, Technical Efficacy Thesaurus, Application Domain, Technology Topic, Popular Technical Reports.
© 2025 PatSnap. All rights reserved.Legal|Privacy policy|Modern Slavery Act Transparency Statement|Sitemap|About US| Contact US: help@patsnap.com