Granulator
A granulator and pressure roller technology, applied in the direction of raw material extrusion granulation, mold extrusion granulation, etc., can solve the problems of ring die and pressure roller wear, low output, short life, etc., to reduce friction, Increased productivity and reduced wear
- Summary
- Abstract
- Description
- Claims
- Application Information
AI Technical Summary
Problems solved by technology
Method used
Image
Examples
Embodiment Construction
[0025] The present invention will be further described below in conjunction with the examples, but the protection scope of the present invention is not limited only to the examples.
[0026] Such as figure 1 and figure 2 As shown, a granulator includes a base 1, a first motor 3, a second motor 4, a feeding device 10, a feeding pipe 6, a feeding pipe 11, a pressing device 12, a transmission device 2, a feeding trough 7 and The third motor 13.
[0027] Both the transmission device 2 and the first motor 3 are arranged on the base 1, and the pressing device 12 and the first motor 3 are connected through the transmission device 2, and the function of the transmission device 2 is to drive the pressing device 12 to run. The power required for pressing is sent by the first motor 3 and then transmitted to the pressing device 12 through the transmission device 2 .
[0028] The second motor 4 is arranged at the lower end of the feeding pipe 6 , the upper end of the feeding pipe 6 com...
PUM
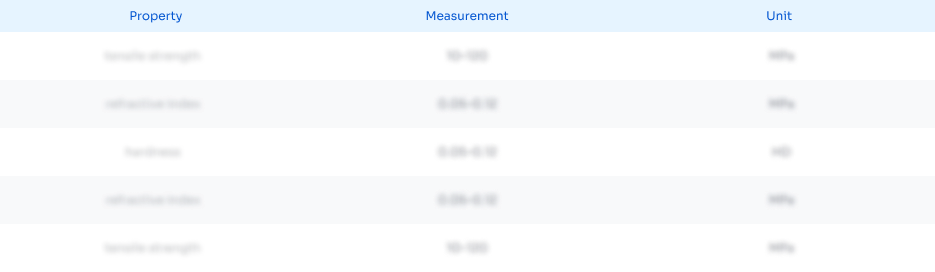
Abstract
Description
Claims
Application Information

- R&D
- Intellectual Property
- Life Sciences
- Materials
- Tech Scout
- Unparalleled Data Quality
- Higher Quality Content
- 60% Fewer Hallucinations
Browse by: Latest US Patents, China's latest patents, Technical Efficacy Thesaurus, Application Domain, Technology Topic, Popular Technical Reports.
© 2025 PatSnap. All rights reserved.Legal|Privacy policy|Modern Slavery Act Transparency Statement|Sitemap|About US| Contact US: help@patsnap.com