Plane shape error evaluating method aiming at precise assembling and based on entropy theory
A technology for plane shape and error evaluation, applied in the direction of measuring devices, instruments, etc., can solve problems such as the influence of assembly accuracy, the inability to reveal the relationship between shape error distribution and assembly accuracy, and different contact states of mating surfaces
- Summary
- Abstract
- Description
- Claims
- Application Information
AI Technical Summary
Problems solved by technology
Method used
Image
Examples
Embodiment Construction
[0047] figure 1 Shown are three parts with the same flatness Δ, when they are used as assembly reference parts and the same ideal planar part P 2 During assembly, due to the three assembly reference parts mating surface A 1 The distribution of the shape error is different, resulting in the assembled parts P 2 Different position errors and direction errors are generated after assembly, such as figure 2 shown, where figure 2(a) is the worst assembly state. Although analyzed from the perspective of geometric error, state (c) is the same as state (b), but because the number of contact points in state (c) is less than that of state (b), under the action of assembly force, the contact area D 1 and D 2 It will produce large elastic-plastic deformation, accompanied by large local contact stress, resulting in P 2 The additional error of deformation caused by deformation, and the non-uniform contact leads to the formation of non-uniform stress field inside the structure. The no...
PUM
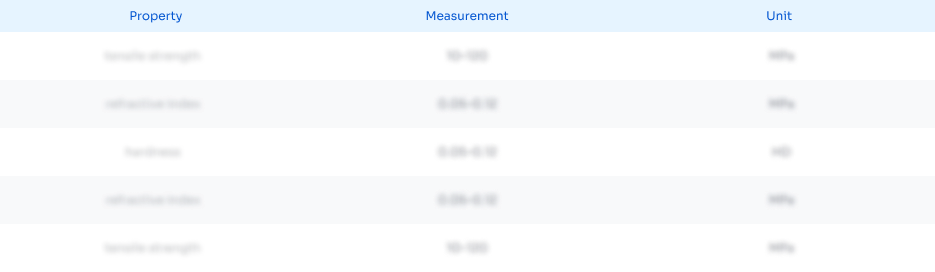
Abstract
Description
Claims
Application Information

- Generate Ideas
- Intellectual Property
- Life Sciences
- Materials
- Tech Scout
- Unparalleled Data Quality
- Higher Quality Content
- 60% Fewer Hallucinations
Browse by: Latest US Patents, China's latest patents, Technical Efficacy Thesaurus, Application Domain, Technology Topic, Popular Technical Reports.
© 2025 PatSnap. All rights reserved.Legal|Privacy policy|Modern Slavery Act Transparency Statement|Sitemap|About US| Contact US: help@patsnap.com