Control device and control method for injection molding machine
A technology for an injection molding machine and a control device, which is applied to the control device and the control field of the injection molding machine, can solve the problems of burr and mold release, the size of the molded product is too large, and the pressure response is oscillated, and the effect of stable pressure control is achieved.
- Summary
- Abstract
- Description
- Claims
- Application Information
AI Technical Summary
Problems solved by technology
Method used
Image
Examples
Embodiment approach 1
[0053] figure 1 It is a figure which shows the structure of the injection molding machine provided with the control apparatus concerning Embodiment 1 of this invention. As shown in the figure, the injection molding machine has a control device 1000 , a motor 1 , an encoder 2 , a coupling 3 , a ball screw 4 , a screw 5 , a load cell 6 , a cylindrical portion 7 , and a mold 8 .
[0054] The motor 1 is driven by current supplied from the control device 1000 . The encoder 2 detects the position and speed of the motor 1 and outputs the detection results as a position detection value 101 and a speed detection value 102 . The coupling 3 connects the rotating shaft of the motor 1 and the ball screw 4 . A screw 5 is connected to the ball screw 4 via a load cell 6 , and the screw 5 is used to fill and pressurize the mold 8 with the resin 9 filled in the cylindrical portion 7 . The load cell 6 detects the pressure when the screw 5 extrudes the resin 9 , and outputs the detection resul...
Embodiment approach 2
[0124] In Embodiment 1, the pressure and the position are recorded in step ST4, and the elastic constant K is determined based on the proportional relationship between the position of the motor 1 and the pressure established during the execution of the pressure-holding operation in step ST7. Instead of the position of the motor 1 , motor information other than the position, such as the speed of the motor 1 or the acceleration of the motor 1 , may be used.
[0125] The control device of Embodiment 2 uses the speed of the motor 1 instead of the position of the motor 1 . In addition, the control device of the second embodiment has the same components as those of the first embodiment except for the elastic constant constant unit. here, as Figure 5 As shown, the reference numeral 2000 is assigned to the control device of the second embodiment, and the reference numeral 21 is assigned to the elastic constant constant part of the second embodiment to distinguish them from the first...
Embodiment approach 3
[0145] In Embodiments 1 and 2, the test operation is performed in a continuous period from when the pressure-holding operation judging unit determines that the pressure-holding operation is being performed to when it determines that the pressure-holding operation is not being performed. Control parameters are obtained from the position and pressure data, and the control parameters are set in the pressure control unit after the pressure holding operation is completed (that is, after the above-mentioned continuous period ends). On the other hand, according to the control method of Embodiment 3, the elastic constant K is determined successively during the continuous period in which it is determined that the pressure maintaining operation is being performed and the filling / pressure maintaining determination unit 17 is determining that the pressure maintaining operation is being performed. Based on this information, the control parameters of the pressure control are updated at any t...
PUM
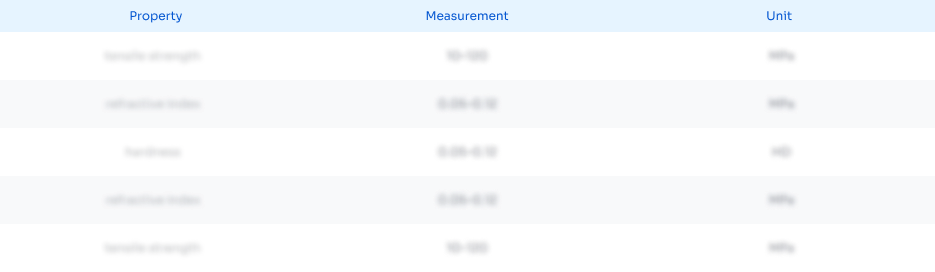
Abstract
Description
Claims
Application Information

- R&D
- Intellectual Property
- Life Sciences
- Materials
- Tech Scout
- Unparalleled Data Quality
- Higher Quality Content
- 60% Fewer Hallucinations
Browse by: Latest US Patents, China's latest patents, Technical Efficacy Thesaurus, Application Domain, Technology Topic, Popular Technical Reports.
© 2025 PatSnap. All rights reserved.Legal|Privacy policy|Modern Slavery Act Transparency Statement|Sitemap|About US| Contact US: help@patsnap.com