A method for controlling boiler combustion conditions
A technology of combustion working conditions and control methods, which is applied in the direction of combustion methods, safety devices of combustion chambers, combustion chambers, etc. It can solve problems such as boiler fire extinguishing, safety accidents, and difficulty in accurately grasping the timing of oil injection and stable combustion, so as to make it difficult to make mistakes , the effect of reducing the monitoring burden
- Summary
- Abstract
- Description
- Claims
- Application Information
AI Technical Summary
Problems solved by technology
Method used
Image
Examples
Embodiment 1
[0023] Embodiment one, see figure 1 .
[0024] A control method for boiler combustion conditions, characterized in that,
[0025] Step 101, receiving the combustion working condition signal;
[0026] The combustion condition signal may include parameter signals that can reflect the combustion condition of the boiler, such as furnace negative pressure value, differential fluctuation value of steam drum pressure, or burner fire detection change times, etc.
[0027] Step 102, comparing the combustion condition signal received in step 101 with the preset stable combustion standard;
[0028] The preset stable combustion standard is different according to the type of the combustion working condition signal received, that is, the stable combustion standard corresponds to the type of the combustion working condition signal. For example, when the combustion working condition signal is the furnace negative pressure value, the stable combustion standard is that the instantaneous fluct...
Embodiment 2
[0033] Step 201, receiving the furnace negative pressure value;
[0034] Step 202, comparing the received furnace negative pressure value with the preset furnace negative pressure value;
[0035] Step 203 , when the instantaneous fluctuation value of the furnace negative pressure exceeds ±300 Pa, issue a stable combustion command.
[0036] Furnace negative pressure refers to the flue gas pressure at the top of the furnace, which is one of the important parameters reflecting the stability of the combustion conditions. Once the combustion conditions in the furnace change, the furnace negative pressure will change accordingly. . When the negative pressure of the furnace is too large, the air leakage increases, the power consumption of the suction fan, the loss of incomplete combustion, and the heat loss of exhaust smoke all increase. It even makes the combustion unstable and even the negative pressure of the fire extinguishing furnace is small or even becomes positive.
[0037...
Embodiment 3
[0039] Step 301, receiving the differential fluctuation value of the drum pressure;
[0040] Step 302, comparing the received differential fluctuation value of the drum pressure with the preset differential fluctuation value of the drum pressure;
[0041] Step 303, when the differential fluctuation value of the drum pressure exceeds ±3, issue a steady combustion command.
[0042] The dynamic pressure fluctuation in the steam drum is small, but the pressure fluctuation in the ascending and descending pipes, water wall, etc. is relatively large, which cannot reflect the instantaneous pressure performance value of the boiler, so the steam drum pressure should be used as the differential signal input regulator. The differential fluctuation value of the drum pressure represents the change of the boiler heat storage when the working conditions change. When the boiler combustion rate increases, the change of the steam flow has a certain inertia, but the differential fluctuation of th...
PUM
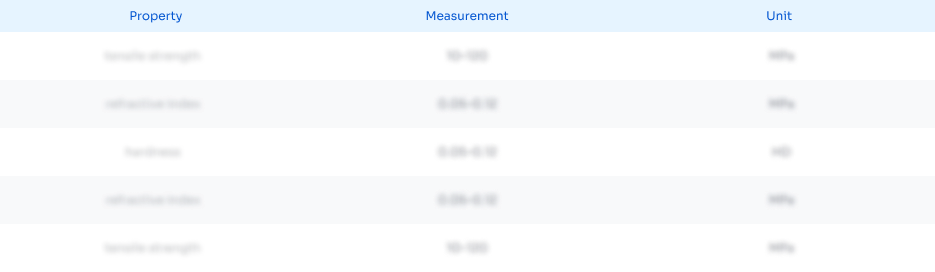
Abstract
Description
Claims
Application Information

- R&D
- Intellectual Property
- Life Sciences
- Materials
- Tech Scout
- Unparalleled Data Quality
- Higher Quality Content
- 60% Fewer Hallucinations
Browse by: Latest US Patents, China's latest patents, Technical Efficacy Thesaurus, Application Domain, Technology Topic, Popular Technical Reports.
© 2025 PatSnap. All rights reserved.Legal|Privacy policy|Modern Slavery Act Transparency Statement|Sitemap|About US| Contact US: help@patsnap.com