Three-dimensional interface stress sensor
A stress sensor and three-dimensional interface technology, applied in the direction of instruments, measuring force, measuring devices, etc., can solve the problems of large geometric size, difficulty in integrating sensor arrays, complex peripheral circuits, etc., to reduce geometric size, simplify peripheral circuits, increase Effect of large measuring range
- Summary
- Abstract
- Description
- Claims
- Application Information
AI Technical Summary
Problems solved by technology
Method used
Image
Examples
Embodiment Construction
[0029] Below in conjunction with specific embodiment, further illustrate the present invention. It should be understood that these examples are only used to illustrate the present invention and are not intended to limit the scope of the present invention. In addition, it should be understood that after reading the teachings of the present invention, those skilled in the art can make various changes or modifications to the present invention, and these equivalent forms also fall within the scope defined by the appended claims of the present application.
[0030] refer to figure 1 and refer to figure 2 , the sensor described in the present invention is mainly composed of a top layer 1 , a driving electrode 2 , an intermediate layer 3 , a sensing electrode 4 and a bottom layer 5 . in:
[0031] The top layer 1 and the bottom layer 5 are PCB boards with a square shape and a size of 1cm×1cm, but not limited to this shape and size. Here, PCB boards are used to facilitate the coupl...
PUM
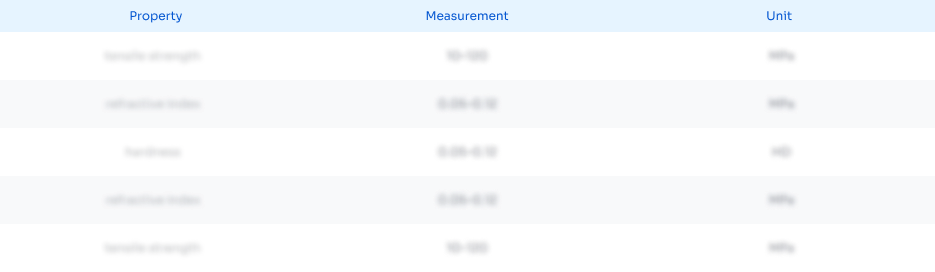
Abstract
Description
Claims
Application Information

- Generate Ideas
- Intellectual Property
- Life Sciences
- Materials
- Tech Scout
- Unparalleled Data Quality
- Higher Quality Content
- 60% Fewer Hallucinations
Browse by: Latest US Patents, China's latest patents, Technical Efficacy Thesaurus, Application Domain, Technology Topic, Popular Technical Reports.
© 2025 PatSnap. All rights reserved.Legal|Privacy policy|Modern Slavery Act Transparency Statement|Sitemap|About US| Contact US: help@patsnap.com