Rotary type magneto-rheological damper
A magneto-rheological damper, a rotary technology, applied in non-rotational vibration suppression, vibration suppression adjustment, etc., can solve the problems of failure to use the rotor end face, large axial size, complex structure, etc., and achieve easy design and calculation, magnetic induction The effect of uniform strength and increased working area
- Summary
- Abstract
- Description
- Claims
- Application Information
AI Technical Summary
Problems solved by technology
Method used
Image
Examples
Embodiment Construction
[0014] Further describe the present invention below in conjunction with embodiment and accompanying drawing thereof.
[0015] The rotary magneto-rheological damper designed by the present invention (referred to as the damper, see Figure 1-4 ), the damper mainly includes a front end cover 1, a rear end cover 2, a front excitation coil 3, a rear excitation coil 4, a rotor 5, a bearing 6, a sealing ring 7, a sealing ring 8, a magnetic isolation ring 9 and a casing 10.
[0016] The front end cover 1 and the rear end cover 2 of the damper of the present invention are located on both sides of the rotor 5, and the front end cover 1 and the rear end cover 2 are respectively connected with the shell 10 by screws to form a stator. Between the rotor 5 and the front end cover 1 and between the rotor 5 and the rear end cover 2, bearings 6 and sealing rings 7 are respectively placed; the front excitation coil 3 is wound in the front end cover 1, and the rear excitation coil 4 is wound in t...
PUM
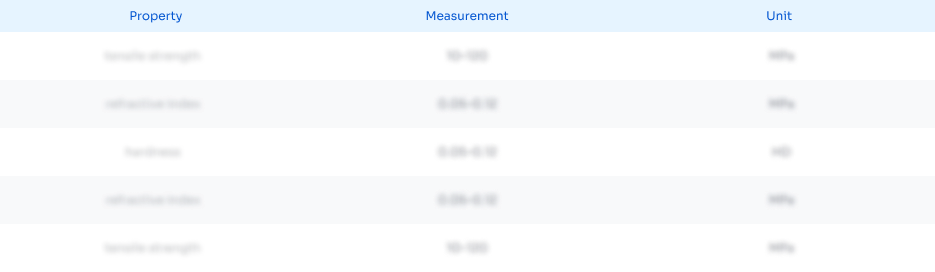
Abstract
Description
Claims
Application Information

- R&D
- Intellectual Property
- Life Sciences
- Materials
- Tech Scout
- Unparalleled Data Quality
- Higher Quality Content
- 60% Fewer Hallucinations
Browse by: Latest US Patents, China's latest patents, Technical Efficacy Thesaurus, Application Domain, Technology Topic, Popular Technical Reports.
© 2025 PatSnap. All rights reserved.Legal|Privacy policy|Modern Slavery Act Transparency Statement|Sitemap|About US| Contact US: help@patsnap.com