Self-measurement piezoelectric stack pump
A piezoelectric stacking and self-measurement technology, which is applied in the direction of pumps, pumps with flexible working elements, liquid variable capacity machinery, etc., can solve the problems of accuracy and reliability of measurement accuracy, and achieve accurate measurement accuracy The effect of high accuracy and reliability and simple structure
- Summary
- Abstract
- Description
- Claims
- Application Information
AI Technical Summary
Problems solved by technology
Method used
Image
Examples
Embodiment Construction
[0018] The valve cover 2 is installed on the pump cover 4 through screws, and the pump cover 4 is installed on the pump body 10 through screws; a cantilever beam type outlet valve 1 and an inlet valve are bonded between the valve cover 2 and the pump cover 4 3. The outlet valve 1 is formed by bonding the piezoelectric film 1-1 and the substrate 1-2, and the inlet valve 3 is formed by bonding the piezoelectric film 3-1 and the substrate 3-2; in the pump cover 4 A pump chamber diaphragm 8 is crimped between the pump body 10, and a piston 7 and a top block 9 are installed on both sides of the pump chamber diaphragm 8 through screws; the piston 7 and the sealing ring 6 installed on the piston 7 , the pump cover 4, the outlet valve 1 and the inlet valve 3 together constitute the pump chamber 5; the bolt 13 installed at the end of the pump body 10 presses the piezoelectric stack driver 11 on the top block 9 through the anti-twist block 12 ; The piezoelectric stack driver 11, the out...
PUM
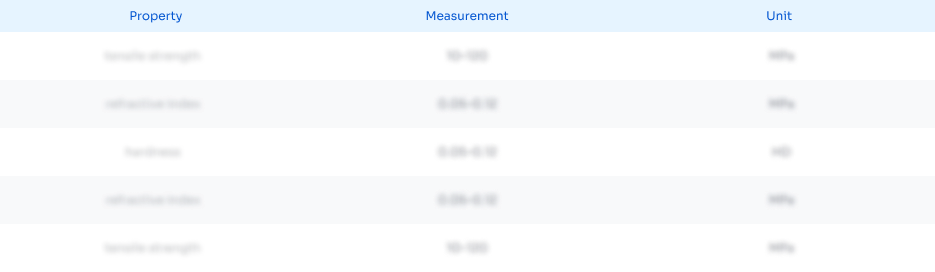
Abstract
Description
Claims
Application Information

- R&D
- Intellectual Property
- Life Sciences
- Materials
- Tech Scout
- Unparalleled Data Quality
- Higher Quality Content
- 60% Fewer Hallucinations
Browse by: Latest US Patents, China's latest patents, Technical Efficacy Thesaurus, Application Domain, Technology Topic, Popular Technical Reports.
© 2025 PatSnap. All rights reserved.Legal|Privacy policy|Modern Slavery Act Transparency Statement|Sitemap|About US| Contact US: help@patsnap.com