POSS/PA6 (polyhedral oligomeric silsesquioxane/polycaprolactam) composite material and preparation method thereof
A composite material and cage technology, applied in the direction of silicon organic compounds, etc., can solve the problems of affecting the improvement of mechanical properties such as low temperature impact toughness of modified PA6, affecting the dispersion of POSS monomers, and limited addition of POSS, etc., to improve the application temperature. range, low thermal conductivity, effect of improving dispersibility
- Summary
- Abstract
- Description
- Claims
- Application Information
AI Technical Summary
Problems solved by technology
Method used
Image
Examples
Embodiment 1
[0051] (1) Add 70ml of γ-(2,3-epoxypropoxy)propyltrimethoxysilane and 10ml of phenyltrimethoxysilane into a 250ml one-necked flask, then add 150ml of ethanol to it, and then Add concentrated hydrochloric acid dropwise to the aforementioned mixed solution, adjust the pH value to about 3, raise the temperature to 90°C and react for 7 days; filter after the reaction, and vacuum-dry at 80°C for 24 hours to obtain the POSS product with the structure of formula (1);
[0052] (2) Air-dry PA6 at 100°C for 3 hours;
[0053] (3) Weigh 99 parts of PA6 dried in (2) and 1 part of POSS prepared in (1), 0.2 parts of tetraerythritol ester antioxidant, 0.2 parts of tris(2,4-di-tert-butylphenyl) phosphite Ester antioxidant, 0.5 part of montan wax, mixed in a high-speed mixer for 5 minutes;
[0054] (4) Extrude and granulate the uniformly mixed materials in a twin-screw extruder to obtain POSS / PA6 composite materials; the temperature of the extruder is set to: 190°C for zone I, 215°C for zone I...
Embodiment 2
[0056] (1) Add 70ml of γ-(2,3-glycidoxy)propyltrimethoxysilane and 10ml of cyclopentyltrimethoxysilane into a 250ml one-necked flask, and then add 150ml of methanol to it, Then add concentrated hydrochloric acid dropwise to the aforementioned mixed solution, adjust the pH value to about 3, heat up to 90°C and react for 7 days; filter after the reaction, and vacuum-dry at 80°C for 24 hours to obtain the POSS product with the structure of formula (1);
[0057] (2) Air-dry PA6 at 150°C for 4 hours;
[0058] (3) Weigh 95 parts of PA6 dried in (2) and 5 parts of POSS prepared in (1), 0.2 parts of tris(2,4-di-tert-butylphenyl) phosphite antioxidant, 0.5 parts of pentaerythritol hard Fatty acid ester, 0.5 white wax oil, mixed in a high-speed mixer for 5 minutes;
[0059] (4) Extrude and granulate the uniformly mixed materials in a twin-screw extruder to obtain POSS / PA6 composite materials; the temperature of the extruder is set to: 190°C in zone I, 215°C in zone II, 235°C in zone II...
Embodiment 3
[0061] (1) Add 60ml of γ-(2,3-epoxypropoxy)propyltrimethoxysilane and 20ml of phenyltrimethoxysilane into a 250ml one-necked flask, then add 150ml of ethanol to it, and then Concentrated hydrochloric acid was added dropwise to the aforementioned mixed solution to adjust the pH value to about 3, and the temperature was raised to 90°C to react for 7 days; after the reaction was completed, it was filtered and vacuum-dried at 80°C for 24 hours to obtain the POSS product with the structure of formula (2).
[0062] (2) Air-dry PA6 at 100°C for 3 hours;
[0063] (3) Weigh 90 parts of PA6 dried in (2) and 10 parts of POSS prepared in (1), 0.2 parts of tris(2,4-di-tert-butylphenyl) phosphite antioxidant, 0.2 parts of N, N'-hexamethylenebis(3,5-di-tert-butyl-4-hydroxyphenylpropionamide) antioxidant, 0.5 parts of montan wax, mixed in a high-speed mixer for 5 minutes;
[0064] (4) Extrude and granulate the uniformly mixed materials in a twin-screw extruder to obtain POSS / PA6 composite ma...
PUM
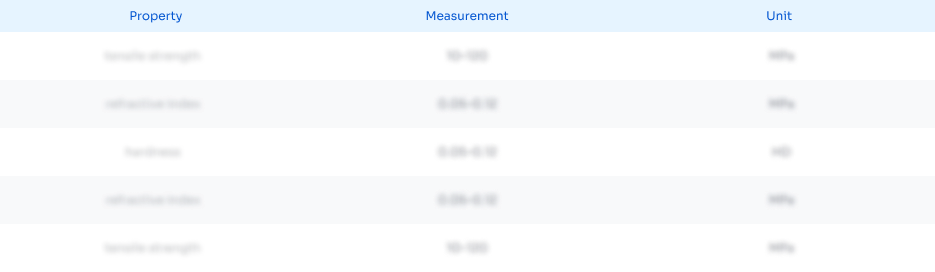
Abstract
Description
Claims
Application Information

- R&D
- Intellectual Property
- Life Sciences
- Materials
- Tech Scout
- Unparalleled Data Quality
- Higher Quality Content
- 60% Fewer Hallucinations
Browse by: Latest US Patents, China's latest patents, Technical Efficacy Thesaurus, Application Domain, Technology Topic, Popular Technical Reports.
© 2025 PatSnap. All rights reserved.Legal|Privacy policy|Modern Slavery Act Transparency Statement|Sitemap|About US| Contact US: help@patsnap.com