Method and equipment for rapid collection and purification of polycrystalline silicon through directional solidification of tailing
A directional solidification, polysilicon technology, applied in chemical instruments and methods, silicon compounds, inorganic chemistry, etc., can solve the problems of reduced industrial production cost, high cost of cutting equipment, affecting purification effect, etc. Consumption and reduce the effect of process links
- Summary
- Abstract
- Description
- Claims
- Application Information
AI Technical Summary
Problems solved by technology
Method used
Image
Examples
Embodiment 1
[0024] like figure 1 The equipment used for the rapid collection and purification of polysilicon by directional solidification tailings shown has an outer wall formed by a vacuum chamber 2, and a vacuum pipeline 15 is installed on the outer wall. The chamber draws a vacuum.
[0025] A ventilation pipeline 13 is fixedly installed on the outer wall, and the ventilation pipeline is used to fill the vacuum chamber with gas, such as inert gas, etc., and the water cooling plate 12 is movably installed at the bottom of the vacuum chamber 2. It can rise or fall according to the set speed. The graphite plate 11 is placed on the top of the water cooling plate. There are 4 holes on the graphite plate 11. One end of the graphite pillar 10 is nested and connected with the graphite plate 11 through the hole, and the other end is nested with the graphite tray 9 Sleeve connection, there is a card slot on the graphite tray, which is conducive to the nested connection between the graphite pill...
Embodiment 2
[0033] Use the equipment described in Example 1 to take the tailings and carry out directional solidification to purify polysilicon. First, add silicon material with a purity of 99.0% of the volume of the crucible to the crucible 7, close the ventilation line 13, and turn on the vacuum pump group 15. The vacuum degree in the vacuum chamber 2 is pumped to 10Pa, close the vacuum pump group 14, open the ventilation pipeline, fill the vacuum chamber 2 with 99.91% argon until the pressure reaches 500Pa, and close the ventilation pipeline;
[0034] The second step of smelting and solidification: turn on the power, use the induction coil 5 and the graphite heating element 6 to heat the silicon material in the crucible 7 to 1450 ° C until it is completely melted into a silicon melt, keep it at this temperature for 30 minutes, and pull it vertically downward The water cooling plate 12 makes the silicon melt in the crucible 7 move vertically downward at a constant speed at a speed of 2.0...
Embodiment 3
[0037] Use the equipment described in Example 1 to take the tailings and carry out directional solidification to purify polysilicon. First, add silicon material with a purity of 99.3% to the crucible 7 with a volume of 92% of the crucible, close the ventilation line 13, and turn on the vacuum pump group 15. The vacuum in the vacuum chamber 2 is pumped to 2 Pa, the vacuum pump group 14 is closed, the ventilation pipeline is opened, and the vacuum chamber 2 is filled with argon gas with a purity of 99.96% until the pressure reaches 5000 Pa, and the ventilation pipeline is closed;
[0038] The second step of smelting and solidification: turn on the power, use the induction coil 5 and the graphite heating element 6 to heat the silicon material in the crucible 7 to 1550 ° C until it is completely melted into a silicon melt, keep it at this temperature for 45 minutes, and pull it vertically downward The water cooling plate 12 makes the silicon melt in the crucible 7 move vertically d...
PUM
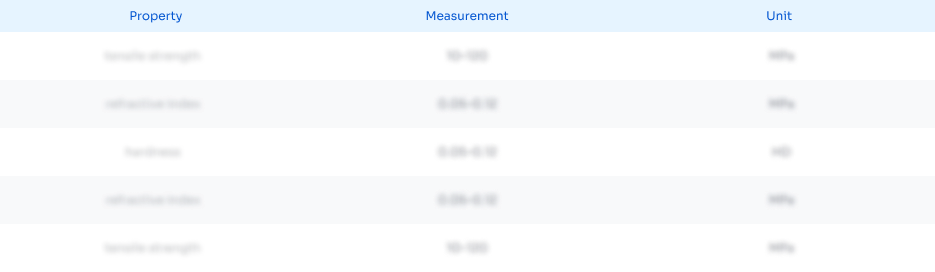
Abstract
Description
Claims
Application Information

- R&D
- Intellectual Property
- Life Sciences
- Materials
- Tech Scout
- Unparalleled Data Quality
- Higher Quality Content
- 60% Fewer Hallucinations
Browse by: Latest US Patents, China's latest patents, Technical Efficacy Thesaurus, Application Domain, Technology Topic, Popular Technical Reports.
© 2025 PatSnap. All rights reserved.Legal|Privacy policy|Modern Slavery Act Transparency Statement|Sitemap|About US| Contact US: help@patsnap.com