Mechatronics Design Method for 65m Aperture Large Reflector Antenna Structure
A technology of antenna structure and design method, applied in computing, electrical digital data processing, special data processing applications, etc., can solve the problems of not reflecting the real influence relationship of the antenna structure and difficult structural deformation.
- Summary
- Abstract
- Description
- Claims
- Application Information
AI Technical Summary
Problems solved by technology
Method used
Image
Examples
Embodiment Construction
[0071] The present invention will be described in further detail below with reference to the accompanying drawings.
[0072] refer to figure 1 , the concrete steps of the present invention are as follows:
[0073] Step 1: Establish a finite element model of a 65m-caliber large-scale reflector antenna.
[0074] According to the basic parameters of antenna diameter D, focal length f, reflective panel, radiation beam, ring beam, and central body, the finite element model of the antenna structure is determined, and the triangular element of the reflective surface and the node theory of the triangular element are obtained under the Cartesian coordinate Oxyz coordinate with n is a natural number greater than 1, such as figure 2 As shown, wherein A is a reflective surface, B is a triangle unit node, and C is a triangular unit. At the same time, the coordinate h of the vertex of the reflective surface in the model coordinate system is determined, and the present invention adopt...
PUM
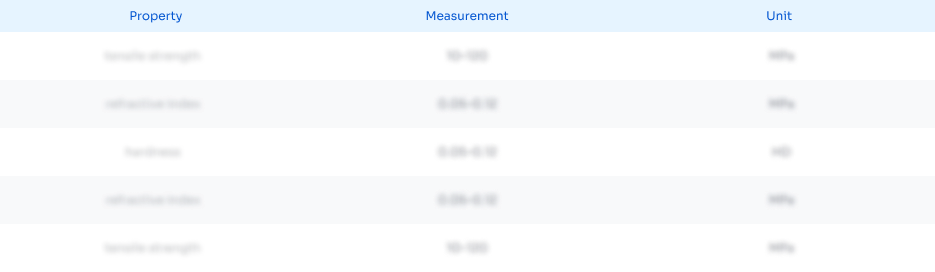
Abstract
Description
Claims
Application Information

- Generate Ideas
- Intellectual Property
- Life Sciences
- Materials
- Tech Scout
- Unparalleled Data Quality
- Higher Quality Content
- 60% Fewer Hallucinations
Browse by: Latest US Patents, China's latest patents, Technical Efficacy Thesaurus, Application Domain, Technology Topic, Popular Technical Reports.
© 2025 PatSnap. All rights reserved.Legal|Privacy policy|Modern Slavery Act Transparency Statement|Sitemap|About US| Contact US: help@patsnap.com