Robot integrated joint location detecting method based on double-rotation change coaxial design
A robot joint and resolver technology, applied in the field of robotics, can solve problems such as low algorithm accuracy, poor reliability, and failure of robot joints
- Summary
- Abstract
- Description
- Claims
- Application Information
AI Technical Summary
Problems solved by technology
Method used
Image
Examples
Embodiment Construction
[0015] In order to make the object, technical solution and advantages of the present invention clearer, the implementation manner of the present invention will be further described in detail below in conjunction with the accompanying drawings.
[0016] figure 1 A kind of robot joint based on the permanent magnet synchronous motor proposed by the present invention, the interior of the joint includes the following components: motor housing 1; motor side rotary transformer stator 2; motor side rotary transformer rotor 3; permanent magnet synchronous motor stator 4; permanent magnet synchronous motor stator 4; Magnetic synchronous motor rotor 5; joint output side casing 6; harmonic reducer steel wheel 7; harmonic reducer wave generator 8; harmonic reducer flexible wheel 9; joint output side resolver stator 10; joint output side resolver Rotor 11; joint right gear cover 12; hollow shaft positioning pin 13; motor bearing 14; bearing mount 15; motor main shaft 16; bearing mount 17; m...
PUM
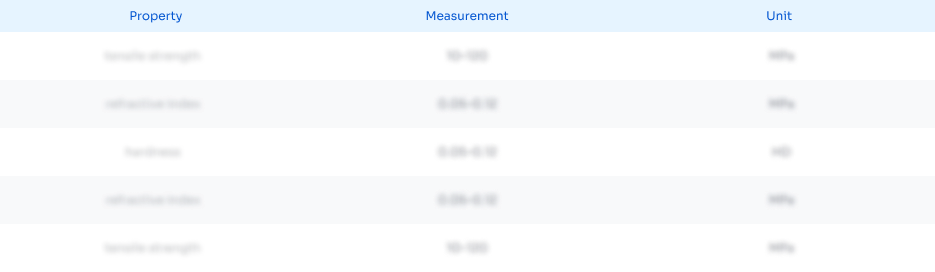
Abstract
Description
Claims
Application Information

- R&D
- Intellectual Property
- Life Sciences
- Materials
- Tech Scout
- Unparalleled Data Quality
- Higher Quality Content
- 60% Fewer Hallucinations
Browse by: Latest US Patents, China's latest patents, Technical Efficacy Thesaurus, Application Domain, Technology Topic, Popular Technical Reports.
© 2025 PatSnap. All rights reserved.Legal|Privacy policy|Modern Slavery Act Transparency Statement|Sitemap|About US| Contact US: help@patsnap.com