Optimization design method for blade root of compound propeller blade
A composite material and propeller blade technology, applied in the direction of calculation, special data processing applications, instruments, etc., can solve the problems that the blade and the propeller hub cannot meet the use requirements, the diameter of the propeller hub is small, and achieve the design method is simple and easy to connect. The effect of firmness and extended service life
- Summary
- Abstract
- Description
- Claims
- Application Information
AI Technical Summary
Problems solved by technology
Method used
Image
Examples
specific Embodiment approach 1
[0025] Specific implementation mode one: combine figure 1 and figure 2 To illustrate this embodiment, the specific steps of a composite material propeller blade root design method described in this embodiment are as follows:
[0026] Step 1, increasing the diameter of the top surface and the diameter of the bottom surface of the hub by m times at the same time;
[0027] Step 2, evenly arrange the composite material blades on the enlarged hub, and use the three-dimensional solid configuration software to draw the geometric model of the composite material propeller;
[0028] Step 3. Import the geometric model of the composite material propeller into GAMBIT, the pre-processor of the computational fluid dynamics analysis software, establish the fluid domain, divide the fluid grid, and construct the hydrodynamic model;
[0029] Step 4. On the basis of the hydrodynamic calculation model that has been constructed, the hydrodynamic performance of the composite propeller is calculat...
specific Embodiment approach 2
[0044] Specific implementation mode two: combination figure 1 and figure 2 To illustrate this embodiment, m=1.05, 1.1, 1.15, 1.2 in Step 1 of a method for optimal design of a composite propeller blade root described in this embodiment. Other components and connections are the same as those in the first embodiment.
PUM
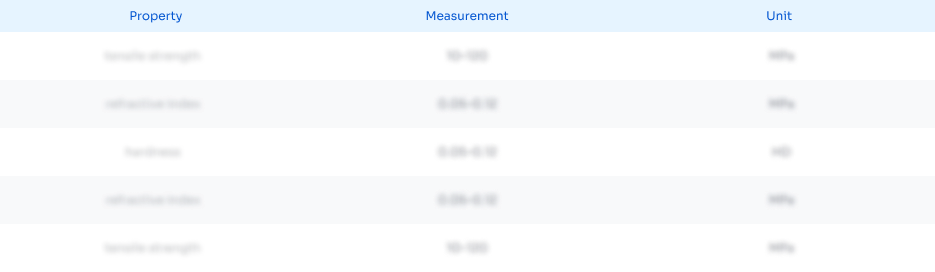
Abstract
Description
Claims
Application Information

- Generate Ideas
- Intellectual Property
- Life Sciences
- Materials
- Tech Scout
- Unparalleled Data Quality
- Higher Quality Content
- 60% Fewer Hallucinations
Browse by: Latest US Patents, China's latest patents, Technical Efficacy Thesaurus, Application Domain, Technology Topic, Popular Technical Reports.
© 2025 PatSnap. All rights reserved.Legal|Privacy policy|Modern Slavery Act Transparency Statement|Sitemap|About US| Contact US: help@patsnap.com