Stealth exhaust system
An exhaust system and cross-section technology, which is applied to the exhaust port of the power plant, jet propulsion device, machine/engine, etc., can solve the problems of increasing exhaust loss, affecting the layout of the whole machine, and reducing the adaptability of the nozzle. Achieve the requirements of reducing the layout space, improve the radar stealth performance, and improve the effect of infrared stealth performance
- Summary
- Abstract
- Description
- Claims
- Application Information
AI Technical Summary
Problems solved by technology
Method used
Image
Examples
Embodiment Construction
[0013] A full understanding of the invention can be obtained from the detailed description and accompanying drawings;
[0014] figure 1 It is a side view of a stealth exhaust system 10 according to an embodiment of the present invention. The stealth exhaust system 10 is composed of an exhaust system inlet 12 , a first S-bend control section 14 , a second S-bend control section 16 , a nozzle throat section 18 , a nozzle side wall 19 and a nozzle 20 . The stealth exhaust system 10 is connected to the jet aircraft engine at the inlet 12 of the exhaust system, and the central line 11 of the inlet section coincides with the axis of the engine. The high-temperature and high-pressure exhaust gas flow generated by the engine enters the stealth exhaust system 10 through the exhaust system inlet 12 , and flows in the pipe surrounded by the nozzle side wall 19 . Engine exhaust flows through the first S-curve control section 14 and the second S-curve control section 16 in sequence, and ...
PUM
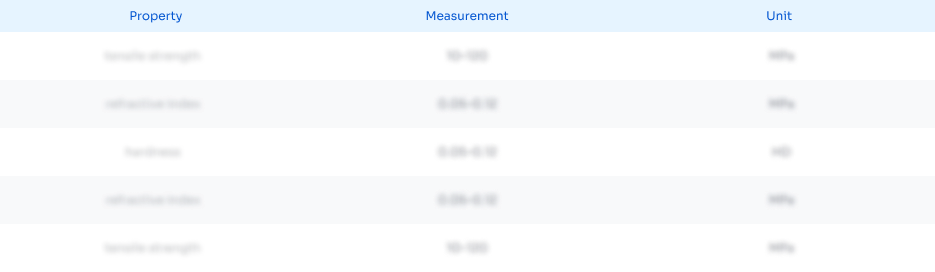
Abstract
Description
Claims
Application Information

- R&D
- Intellectual Property
- Life Sciences
- Materials
- Tech Scout
- Unparalleled Data Quality
- Higher Quality Content
- 60% Fewer Hallucinations
Browse by: Latest US Patents, China's latest patents, Technical Efficacy Thesaurus, Application Domain, Technology Topic, Popular Technical Reports.
© 2025 PatSnap. All rights reserved.Legal|Privacy policy|Modern Slavery Act Transparency Statement|Sitemap|About US| Contact US: help@patsnap.com