Submerged arc welding method for K-shaped groove of 80mm extra-thick steel plate with excellent plate shape after welding
A technology of K-shaped groove and extra-thick steel plate, which is applied to welding equipment, arc welding equipment, and the edge of workpieces, etc., can solve the problems of large residual stress of weld seam, fast cooling speed, high labor intensity, etc., and reduce the number of turning times , welding operation is simple, the effect of reducing labor intensity
- Summary
- Abstract
- Description
- Claims
- Application Information
AI Technical Summary
Problems solved by technology
Method used
Image
Examples
Embodiment 1
[0023] This embodiment is a method for submerged arc welding of 80mm extra-thick steel plate with K-shaped groove with excellent plate shape after welding, which includes the following steps:
[0024] (1) Groove type: K-shaped symmetrical groove is machined, the oblique edge of the front groove and the reverse groove are both 45°, no blunt edge is left at the root, and the groove assembly gap is 2mm;
[0025] (2) Backing welding: when welding, use solid welding wire under pulse current to carry out backing welding of the root bead on the front of the K-groove test plate, so that after the root bead is penetrated, part of the weld metal penetrates the back of the groove to complete the backing. Bottom welding; when welding, a mixed gas of argon and carbon dioxide is used for protection, and the mixed gas is a mixed gas of argon and carbon dioxide, which is a mixed gas with a volume ratio of 80% argon + 20% carbon dioxide;
[0026] (3) After bottoming welding, use submerged arc ...
Embodiment 2
[0030] This embodiment is a method for submerged arc welding of 80mm extra-thick steel plate with K-shaped groove with excellent plate shape after welding, which includes the following steps:
[0031] (1) Groove type: K-shaped symmetrical groove is machined, the oblique edge of the front groove and the reverse groove are both 50°, no blunt edge is left at the root, and the groove assembly gap is 3mm;
[0032] (2) Backing welding: when welding, use solid welding wire under pulse current to carry out backing welding of the root bead on the front of the K-groove test plate, so that after the root bead is penetrated, part of the weld metal penetrates the back of the groove to complete the backing. Bottom welding; when welding, a mixed gas of argon and carbon dioxide is used for protection, and the mixed gas is a mixed gas of argon and carbon dioxide, which is a mixed gas with a volume ratio of 80% argon + 20% carbon dioxide;
[0033] (3) After bottoming welding, use submerged arc ...
PUM
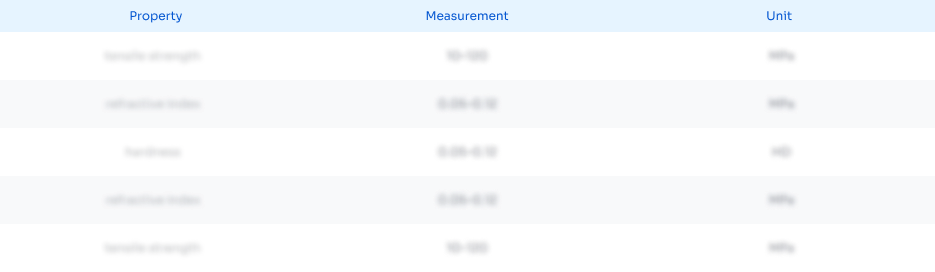
Abstract
Description
Claims
Application Information

- R&D
- Intellectual Property
- Life Sciences
- Materials
- Tech Scout
- Unparalleled Data Quality
- Higher Quality Content
- 60% Fewer Hallucinations
Browse by: Latest US Patents, China's latest patents, Technical Efficacy Thesaurus, Application Domain, Technology Topic, Popular Technical Reports.
© 2025 PatSnap. All rights reserved.Legal|Privacy policy|Modern Slavery Act Transparency Statement|Sitemap|About US| Contact US: help@patsnap.com