Brazing method for turbine rotor assembly of engine
A technology of turbine rotor and brazing method, applied in welding equipment, auxiliary devices, metal processing equipment, etc., can solve problems such as difficulty in welding, and achieve the effects of brazing quality assurance, making up for difficult welding, and enhancing gap filling.
- Summary
- Abstract
- Description
- Claims
- Application Information
AI Technical Summary
Problems solved by technology
Method used
Image
Examples
Embodiment Construction
[0021] The embodiments of the present invention will be described in detail below with reference to the accompanying drawings, but the present invention can be implemented in many different ways defined and covered by the claims.
[0022] see figure 1 with figure 2 , the preferred embodiment of the present invention provides a brazing method for an engine turbine rotor assembly, the turbine rotor assembly includes a turbine rotor disk 20 with a U-shaped groove 21 and a sealing sleeve 10 matched with the turbine rotor disk 20, the turbine rotor The brazing surface of the disk 20 and the brazing surface of the sealing shaft sleeve 10 are tapered after matching; the brazing method includes the following steps: Step S2: Brazing the brazing surface of the turbine rotor disk 20 and the sealing shaft sleeve 10 The surface is plated with easy-to-weld metal; step S4: wrap sheet-shaped solder on the brazing surface of the sealing shaft sleeve 10; step S6: assemble the turbine rotor di...
PUM
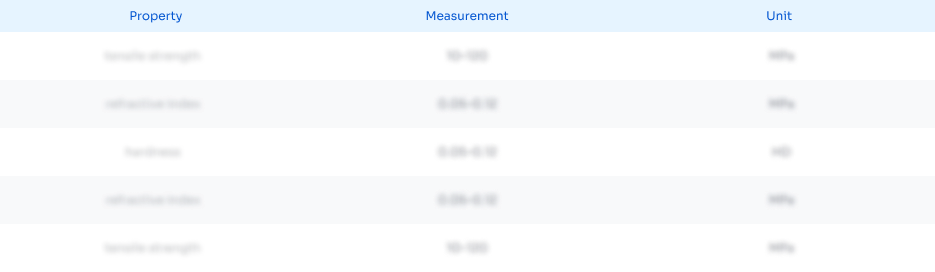
Abstract
Description
Claims
Application Information

- R&D
- Intellectual Property
- Life Sciences
- Materials
- Tech Scout
- Unparalleled Data Quality
- Higher Quality Content
- 60% Fewer Hallucinations
Browse by: Latest US Patents, China's latest patents, Technical Efficacy Thesaurus, Application Domain, Technology Topic, Popular Technical Reports.
© 2025 PatSnap. All rights reserved.Legal|Privacy policy|Modern Slavery Act Transparency Statement|Sitemap|About US| Contact US: help@patsnap.com