High-temperature high-humidity electrode plate curing process
A plate solidification, high temperature and high humidity technology, applied in the direction of lead-acid battery electrodes, etc., can solve the problems of short battery cycle life, long production time, insufficient oxygen supply, etc., to improve the overall performance of the battery, improve the quality of the plate, The effect of shortening the production cycle
- Summary
- Abstract
- Description
- Claims
- Application Information
AI Technical Summary
Problems solved by technology
Method used
Examples
Embodiment 1
[0014] Taking the solidification of a 50Ah raw plate as an example, the specific implementation method of the present invention will be further described below.
[0015] Equipment: A curing room with automatic temperature and humidity control is adopted.
[0016] 1. Hang the paste-coated 50Ah raw plates on the drying rack, and the distance between each green plate is 1mm. Then push the drying rack full of green plates into the curing chamber. Control the temperature of the curing room at 180°C, the relative humidity is 20-30%, and carry out surface drying for about 6 minutes, so that the water content of the raw plate after drying is 8% (weight percentage); 2. Put the curing room The temperature is controlled at 90-95°C, the relative humidity is kept at 100%, and the raw electrode plate is cured for 24 hours.
[0017] After completing the above curing treatment, the test shows that the 4BS content of the plate is 86%.
[0018] Use the above cured plates to assemble a 2V500A...
Embodiment 2
[0019] Embodiment 2: The specific implementation method of the present invention will be further described by taking the curing of a 25Ah raw plate as an example.
[0020] Equipment: A curing room with automatic temperature and humidity control is adopted.
[0021] 1. Hang the paste-coated 25Ah raw plates on the drying rack, and the distance between each green plate is 1mm. Then push the drying rack full of green plates into the curing chamber. Control the temperature of the curing room at 150°C, the relative humidity is 20-30%, and dry the surface for about 4 minutes, so that the water content of the raw plate after drying is 8% (weight percentage); 2. Put the curing room The temperature is controlled at 90-95°C, the relative humidity is kept at 100%, and the raw electrode plate is cured for 24 hours.
[0022] After completing the above curing treatment, the test shows that the 4BS content of the plate is 88%.
[0023] Use the above cured plates to assemble a 2V500Ah batte...
PUM
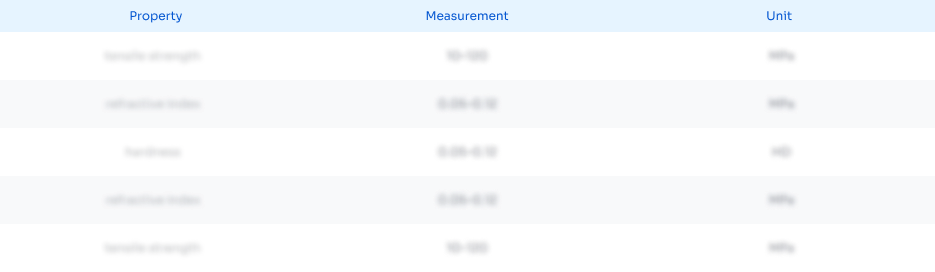
Abstract
Description
Claims
Application Information

- R&D
- Intellectual Property
- Life Sciences
- Materials
- Tech Scout
- Unparalleled Data Quality
- Higher Quality Content
- 60% Fewer Hallucinations
Browse by: Latest US Patents, China's latest patents, Technical Efficacy Thesaurus, Application Domain, Technology Topic, Popular Technical Reports.
© 2025 PatSnap. All rights reserved.Legal|Privacy policy|Modern Slavery Act Transparency Statement|Sitemap|About US| Contact US: help@patsnap.com