Nested disc cam focusing mechanism
A disc cam, nested technology, used in installation, optics, instruments, etc., can solve the problems of machining and assembly errors, cam groove crossing, large errors, etc., to avoid coupling linkage, eliminate return errors, and avoid gaps. Effect
- Summary
- Abstract
- Description
- Claims
- Application Information
AI Technical Summary
Problems solved by technology
Method used
Image
Examples
Embodiment Construction
[0016] Below in conjunction with accompanying drawing, the present invention is described in further detail:
[0017] Such as figure 2 , image 3 , Figure 4 , Figure 5 As shown, the nested disc cam focusing mechanism includes: the first mirror mount 1, the second mirror mount 2, the third mirror mount 3, the fourth mirror mount 4, the fifth mirror mount 5, and the sixth mirror mount 6 , the first connecting rod 7, the second connecting rod 8, the third connecting rod 9, the slider 10, the guide rail 11, the first cam 12, the second cam 13, the third cam 14, the follower 15, the spring 16, the spring Block plate 17, camshaft 18, coupling 19, motor 20. The relative position between the first mirror base 1 and the sixth mirror base 6 remains unchanged, forming the first mirror base group; the relative position between the second mirror base 2 and the fifth mirror base 5 remains unchanged, forming the second mirror base group. Mirror base group; the relative position betwe...
PUM
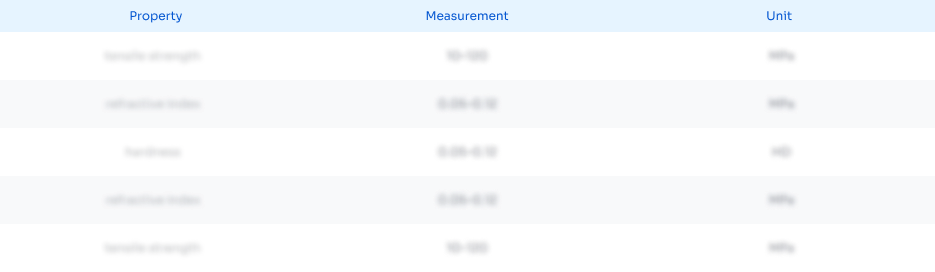
Abstract
Description
Claims
Application Information

- R&D
- Intellectual Property
- Life Sciences
- Materials
- Tech Scout
- Unparalleled Data Quality
- Higher Quality Content
- 60% Fewer Hallucinations
Browse by: Latest US Patents, China's latest patents, Technical Efficacy Thesaurus, Application Domain, Technology Topic, Popular Technical Reports.
© 2025 PatSnap. All rights reserved.Legal|Privacy policy|Modern Slavery Act Transparency Statement|Sitemap|About US| Contact US: help@patsnap.com