Device and method for measuring rotational speed on basis of electrostatic sensor array and data fusion
An electrostatic sensor and data fusion technology, applied to measuring devices, devices using electric/magnetic methods, speed/acceleration/shock measurement, etc., can solve problems such as large temperature errors, high symmetry requirements, and limited measurement range. Achieve the effect of simple structure, easy installation and light weight
- Summary
- Abstract
- Description
- Claims
- Application Information
AI Technical Summary
Problems solved by technology
Method used
Image
Examples
Embodiment Construction
[0024] The invention provides a rotational speed measurement device and method based on an electrostatic sensor array and data fusion. Below in conjunction with accompanying drawing and embodiment the present invention is described as follows:
[0025] figure 1 , 2 Shown is a schematic diagram of the structure and measurement principle of the rotational speed measurement device based on the four-electrode electrostatic sensor array and data fusion. In the figure, the composition of the electrostatic sensor array and the rotational speed measuring device for data fusion: electrostatic sensors 1 are evenly distributed at A, B, C, and D on the periphery of the measured rotating part to form an electrostatic sensor array to sense the location (such as figure 1 , figure 2 , image 3 and Figure 4 A, B, C, D in. E, F, G, H) the rotation information of the rotating parts; the surface of each electrostatic sensor 1 is coated with insulating material 3, which is insulated from t...
PUM
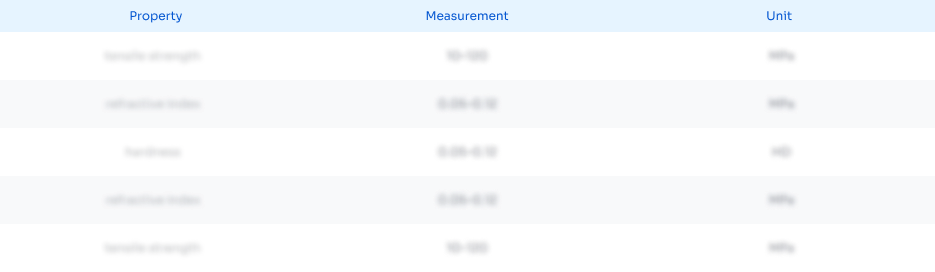
Abstract
Description
Claims
Application Information

- R&D
- Intellectual Property
- Life Sciences
- Materials
- Tech Scout
- Unparalleled Data Quality
- Higher Quality Content
- 60% Fewer Hallucinations
Browse by: Latest US Patents, China's latest patents, Technical Efficacy Thesaurus, Application Domain, Technology Topic, Popular Technical Reports.
© 2025 PatSnap. All rights reserved.Legal|Privacy policy|Modern Slavery Act Transparency Statement|Sitemap|About US| Contact US: help@patsnap.com