Method and device for measuring thickness of wafer
A technology of wafer thickness and measurement method, applied in the field of precision measurement, can solve the problems of affecting measurement accuracy, accuracy impact, and difficulty in unifying measurement data, and achieve the effects of convenient use, improved measurement accuracy, and high measurement accuracy
- Summary
- Abstract
- Description
- Claims
- Application Information
AI Technical Summary
Problems solved by technology
Method used
Image
Examples
Embodiment Construction
[0020] The technical solutions of the present invention will be clearly and completely described below in conjunction with the accompanying drawings of the present invention. Apparently, the described embodiments are only some of the embodiments of the present invention, not all of them. Based on the embodiments of the present invention, all other embodiments obtained by persons of ordinary skill in the art without creative efforts fall within the protection scope of the present invention.
[0021] The wafer thickness measuring method of the embodiment of one aspect of the present invention is characterized in that the wafer is kept in a vertical state during the measurement process, and the vacuum chuck is also vertically arranged. Forced by gravity parallel to the wafer surface.
[0022] In one embodiment of the present invention, the wafer thickness measurement method adopts a touch probe with a horizontal layout, and the right probe of the touch probe moves from the horizo...
PUM
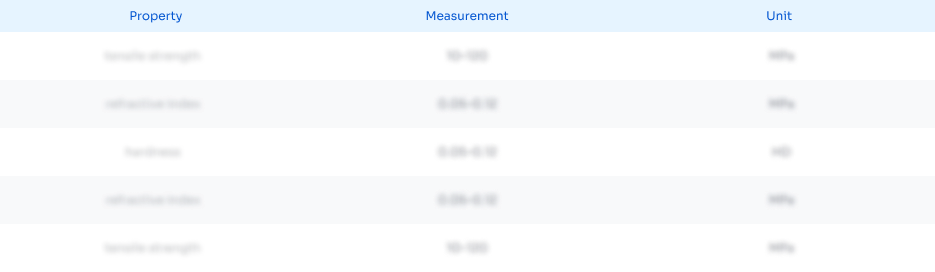
Abstract
Description
Claims
Application Information

- R&D Engineer
- R&D Manager
- IP Professional
- Industry Leading Data Capabilities
- Powerful AI technology
- Patent DNA Extraction
Browse by: Latest US Patents, China's latest patents, Technical Efficacy Thesaurus, Application Domain, Technology Topic, Popular Technical Reports.
© 2024 PatSnap. All rights reserved.Legal|Privacy policy|Modern Slavery Act Transparency Statement|Sitemap|About US| Contact US: help@patsnap.com