Optical film and manufacturing method thereof
A technology of optical diaphragm and manufacturing method, which is applied in the direction of optical elements, other household appliances, household appliances, etc., can solve the problems of high cost, inconvenient manufacture and installation of multiple diaphragms, etc., achieve good thermal expansion and contraction rate, and manufacture And the effect of easy installation and cost reduction
- Summary
- Abstract
- Description
- Claims
- Application Information
AI Technical Summary
Problems solved by technology
Method used
Image
Examples
Embodiment Construction
[0017] See figure 1 . The optical film of the present invention comprises an optical film substrate 1, a prism structure 2 and a microlens structure 3, and the prism structure and the microlens structure are respectively arranged on two opposite surfaces of the optical film substrate. In this specific embodiment, the prism structure 2 is disposed on the upper surface of the optical film substrate 1 , and the microlens structure 3 is disposed on the lower surface of the optical film substrate 1 . The optical film substrate is an optical grade film substrate such as PET or PC. Both the prism structure and the microlens structure are formed on the optical film substrate by rolling and curing UV glue through rollers.
[0018] When used in backlight modules, DBEF (Dual Brightness Enhancement Film, emissive polarizer) 4 can also be added to the optical film, such as figure 2 shown.
[0019] See image 3 , which shows a principle of manufacturing the above-mentioned optical fi...
PUM
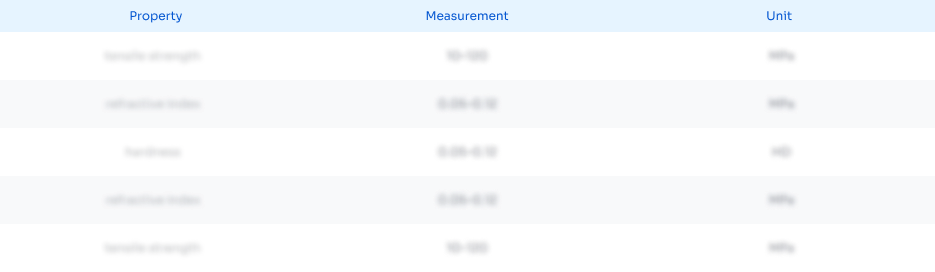
Abstract
Description
Claims
Application Information

- R&D
- Intellectual Property
- Life Sciences
- Materials
- Tech Scout
- Unparalleled Data Quality
- Higher Quality Content
- 60% Fewer Hallucinations
Browse by: Latest US Patents, China's latest patents, Technical Efficacy Thesaurus, Application Domain, Technology Topic, Popular Technical Reports.
© 2025 PatSnap. All rights reserved.Legal|Privacy policy|Modern Slavery Act Transparency Statement|Sitemap|About US| Contact US: help@patsnap.com