Exhaust device used for casting die
A technology for exhaust devices and die-casting molds, which is applied in the direction of valve devices, mechanical equipment, engine components, etc., can solve problems such as interruption of die-casting operations, temperature drop, metal residues, etc., to achieve simple and easy maintenance and management, reduce frictional resistance, Effect of suppressing thermal expansion
- Summary
- Abstract
- Description
- Claims
- Application Information
AI Technical Summary
Problems solved by technology
Method used
Image
Examples
Embodiment 1
[0044] Embodiment 1: The exhaust device for a die-casting mold provided in this preferred embodiment is as attached figure 1 , attached figure 2 shown, with figure 1 Provided that the fixed module 1 is equipped with the situation of the gas delivery device 10, the appended figure 2 is attached figure 1 A-A sectional view of A-A shows the cross-section of the exhaust device. At the same time attached figure 1 It is the top view of the moving module 2 of the exhaust device after it has been folded off. The symbol 1 shows the fixed module for die-casting, the symbol 2 shows the moving module, and the symbol 3 shows the space between the fixed module 1 and the moving module 2. An exhaust passage formed and communicated with the die-casting mold cavity. Marked 4 is a pressure-receiving plunger located at the intake side 13 of the exhaust passage 3, and the pressure-receiving plunger 4 is arranged on the fixed module 1 and can move up and down.
[0045] Marked 5 is a blo...
Embodiment 2
[0047] Embodiment 2: A kind of exhaust device for die-casting mold that this preferred embodiment provides is as attached image 3 , attached Figure 4 As shown, the difference between this preferred embodiment and the first embodiment lies in the formation of the air stagnation portion 9. Obviously, the air stagnation portion 9 may not be formed by cutting the outer circumferences of the pressurized plunger 4 and the lock valve 5 respectively. , but formed by cutting one side of the fixed module 1. Of course, it is also possible to cut the fixed module 1 on one side to form the air stagnation portion 9, and the other side still cuts the outer circumference of the pressure plunger 4 or the lock valve 5 to form the air stagnation portion 9. In this preferred embodiment, the appended Figure 4 The situation shown is that the air retention part 9 on the plunger sliding part 41 on the pressure receiving plunger 4 is formed on the side of the cutting module 1, and the air retentio...
PUM
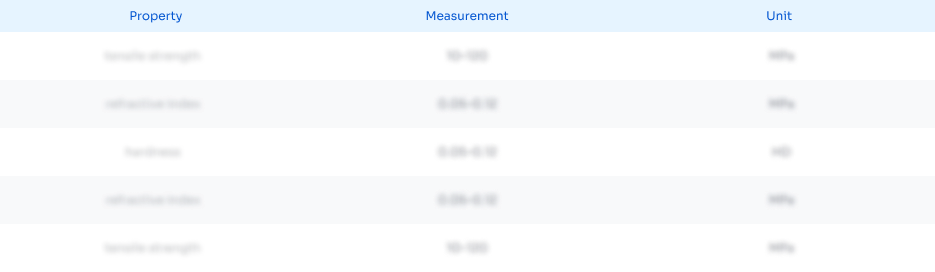
Abstract
Description
Claims
Application Information

- R&D
- Intellectual Property
- Life Sciences
- Materials
- Tech Scout
- Unparalleled Data Quality
- Higher Quality Content
- 60% Fewer Hallucinations
Browse by: Latest US Patents, China's latest patents, Technical Efficacy Thesaurus, Application Domain, Technology Topic, Popular Technical Reports.
© 2025 PatSnap. All rights reserved.Legal|Privacy policy|Modern Slavery Act Transparency Statement|Sitemap|About US| Contact US: help@patsnap.com